Spiral Blade: Core Considerations for Material Selection
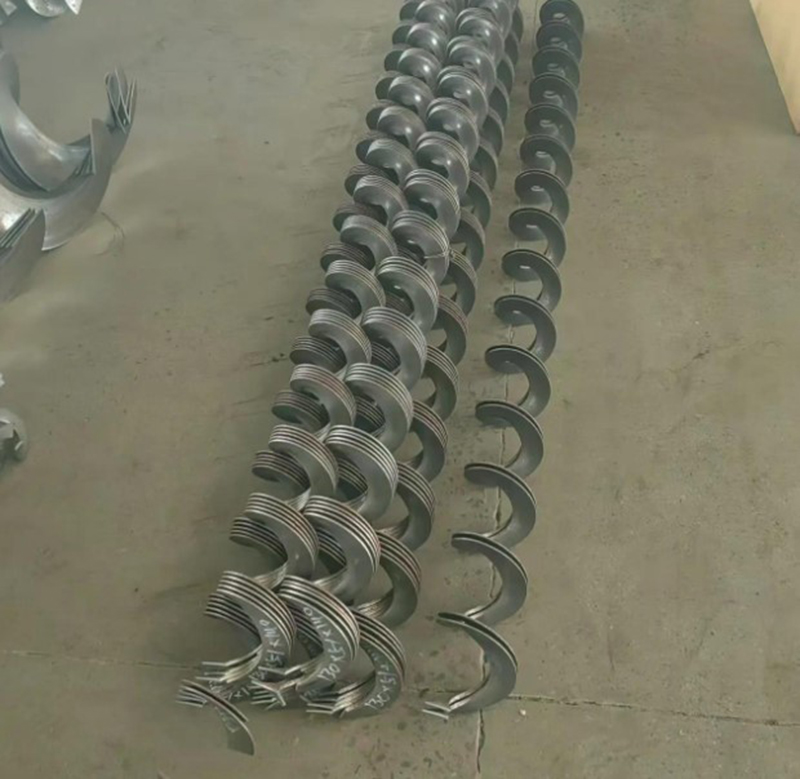

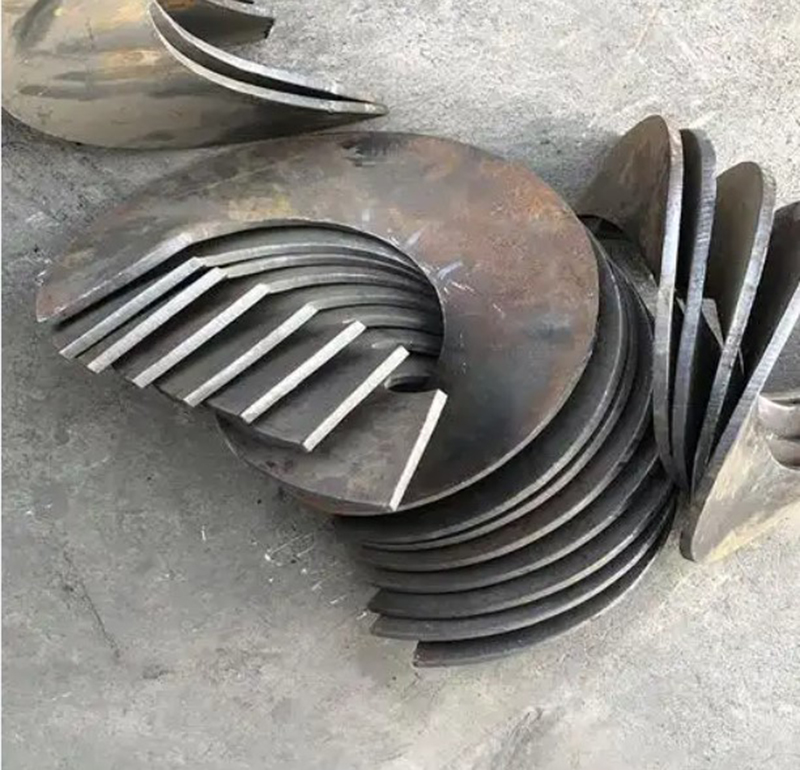
Product name: | Spiral Blade: Core Considerations for Material Selection |
Keywords: | |
Industry: | Metallurgy and minerals - Mining industry |
Process: | - |
Material: |
Processing manufacturer
- There are 34 manufacturers that provide similar products
- There are 143 manufacturers that provide this processing technology
- There are 63 manufacturers that provide this material processing service
- There are 155 manufacturers that provide this industry processing service
Product details
Material Properties (Most Critical!):
Abrasiveness: The content, hardness, and shape of hard particles (sand, metal shavings, glass shards, mineral crystals) in the material. The higher the abrasiveness, the more high-hardness, high-wear-resistant materials are needed (high-chromium cast iron, high-hardness wear-resistant steel, thick hardfacing layer).
Impact Resistance: Does the material contain large, heavy, or hard components (such as large ore, metal components, construction waste)? High impact resistance requires high-toughness materials (high-manganese steel, high-toughness wear-resistant steel such as Hardox 450/500).
Corrosiveness: Does the material contain water, acids, alkalis, salts, or other corrosive chemicals? Corrosion-resistant materials need to be selected (stainless steel, corrosion-resistant grades of wear-resistant steel, engineering plastics).
Viscosity/Entanglement: Is the material prone to sticking (such as wet sludge, clay) or entanglement (such as fibers, plastic bags)? Material surface finish has some influence (such as polished stainless steel, UHMWPE), but it is mainly solved by blade structure design.
Temperature: High-temperature materials (such as hot slag, molten materials) require heat-resistant steel or special alloys (such as 310 stainless steel).
Working Conditions:
Load: The magnitude of the torque, thrust, and extrusion force. High loads require high-strength materials (high-grade wear-resistant steel).
Rotation Speed: High rotation speed exacerbates wear and heat generation.
Operating Environment: Indoor/outdoor? Temperature? Humidity? Is there an explosion risk (explosion-proof design required)? Hygiene level requirements (food grade, GMP)?
Equipment Size and Design: Large, heavy-duty blades require higher toughness and strength of the material; complex structures may limit material selection (such as casting difficulty).
Cost and Maintenance:
Initial Cost: The cost of high-chromium cast iron, high-manganese steel, stainless steel, and hardfacing treatment is much higher than ordinary steel or wear-resistant steel.
Service Life: Although high-wear-resistant materials are expensive, they have a long service life and may be more economical in the long run (calculate life cycle cost LCC).
Maintainability: Hardfaced blades can be repaired on-site; integral cast blades (high-chromium cast iron) can usually only be replaced; wear-resistant steel plate blades can be repaired by hardfacing or replaced after wear.
Replacement Convenience: Is the blade easy to disassemble and replace? Locations where replacement is difficult require longer-life materials.
Similar products
MoreMachining Process Analysis of Carbon Steel Fixed Anchor Plates
- Process : Machining - CNC milling or milling machining
- Material : Carbon steel
Cone Crusher Mantle
- Process : -
- Material :
What are the machining processes used for processing axial fan housings
- Process : Sheet metal - Welding
- Material : Carbon steel
Custom Fabrication of S355JR Welded H-Beams for Construction Projects
- Process : Sheet metal - Welding
- Material : Carbon steel
Drill Stabilizers Applied in Oil Drilling Platforms
- Process : Machining - Five-axis machining
- Material : Alloy steel
Heavy-Walled Flange Milling-Turning Machining and Flaw Detection
- Process : Machining - Turning Milling compound
- Material : Alloy steel
Precision Machining of U-Steel Profiles for Building Applications
- Process : Stamping - General stamping
- Material : Aluminum
Innovative skiving technology: Breaking through the bottleneck of high-density heat dissipation technology
- Process : Surface treatment - Others
- Material : Alloy steel
More products
MoreMachining Process Analysis of Carbon Steel Fixed Anchor Plates
- Process : Machining - CNC milling or milling machining
- Material : Carbon steel
Cone Crusher Mantle
- Process : -
- Material :
What are the machining processes used for processing axial fan housings
- Process : Sheet metal - Welding
- Material : Carbon steel
Custom Fabrication of S355JR Welded H-Beams for Construction Projects
- Process : Sheet metal - Welding
- Material : Carbon steel
Drill Stabilizers Applied in Oil Drilling Platforms
- Process : Machining - Five-axis machining
- Material : Alloy steel
Heavy-Walled Flange Milling-Turning Machining and Flaw Detection
- Process : Machining - Turning Milling compound
- Material : Alloy steel
Precision Machining of U-Steel Profiles for Building Applications
- Process : Stamping - General stamping
- Material : Aluminum
Innovative skiving technology: Breaking through the bottleneck of high-density heat dissipation technology
- Process : Surface treatment - Others
- Material : Alloy steel