Material Selection for Helical Blades
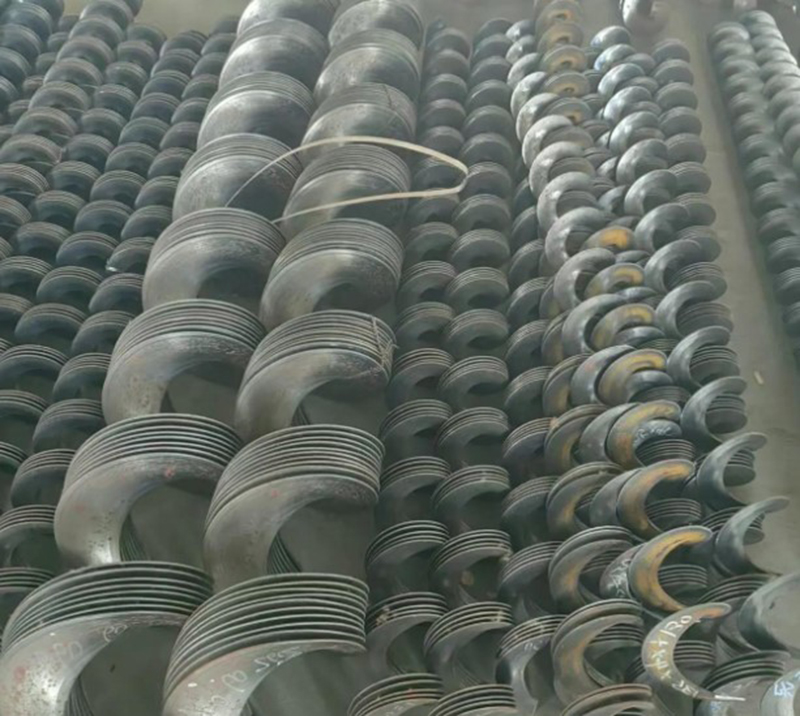
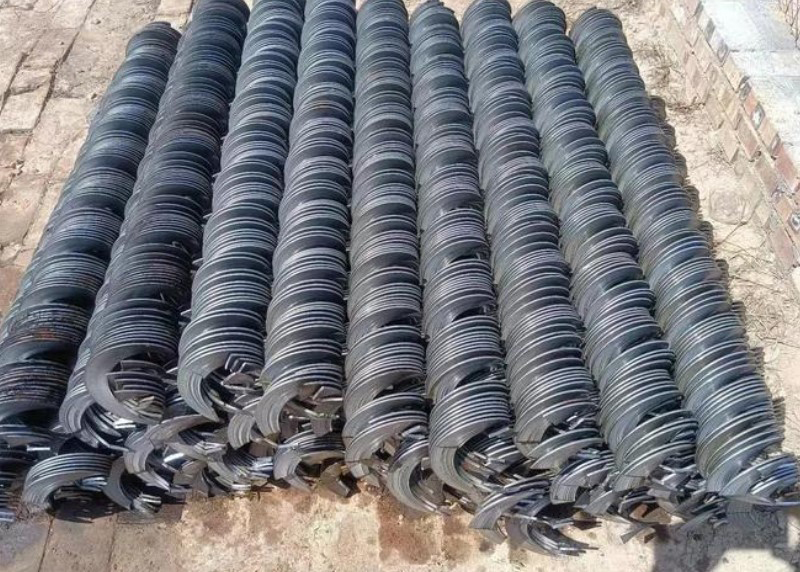
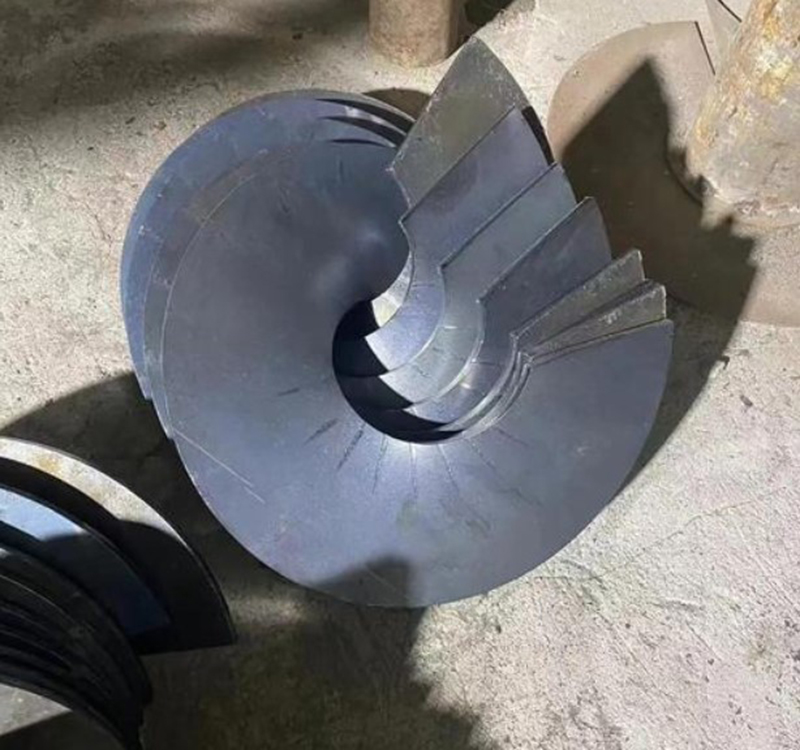
Product name: | Material Selection for Helical Blades |
Keywords: | |
Industry: | Metallurgy and minerals - Metallurgy industry |
Process: | - |
Material: |
Processing manufacturer
- There are 44 manufacturers that provide similar products
- There are 129 manufacturers that provide this processing technology
- There are 90 manufacturers that provide this material processing service
- There are 113 manufacturers that provide this industry processing service
Product details
The material selection for helical blades is a critical determinant of their performance, lifespan, and cost. Faced with complex operating conditions such as severe wear, impact, and corrosion, there is no "one-size-fits-all" material. A comprehensive trade-off must be made based on specific application scenarios, material characteristics, working conditions, and cost budgets. The following is a detailed analysis of the main material categories and their selection logic:
Material Type | Representative Grades | Core Advantages | Main Disadvantages | Typical Application Scenarios |
---|---|---|---|---|
High-Strength Wear-Resistant Steel Plate | Hardox 400/450/500, NM360/400/450, JFE-EH400/500 | Optimal comprehensive performance: High strength, good wear resistance, good toughness, weldability, relatively good machinability, and high cost-effectiveness. | Extreme wear resistance is not as good as high-chromium cast iron; toughness is not as good as high-manganese steel. | Widest range of applications: Crusher blades, conveying moderately abrasive materials (household waste, industrial waste, construction waste, wood, general mineral powder). |
High-Chromium Cast Iron | Cr15, Cr20, Cr26, KmTBCr26 | Top-notch wear resistance: Extremely high hardness (HRC 55-65), extremely strong resistance to abrasive wear. | Extremely poor toughness: High brittleness, easy to break; Poor weldability: Difficult to weld and repair; Difficult to process: Usually cast, high cost. | Pure high-wear, low-impact conditions: Conveying slag, cinder, quartz sand, gravel, industrial solid waste containing a large amount of hard minerals. Use with caution where there is a risk of impact. |
High-Manganese Steel | ZGMn13, ZGMn18Cr2 | Excellent impact toughness: Surface hardens after impact, becoming harder with wear (HBW 500+). | General wear resistance without impact; high cost; work-hardened layer may peel off; welding requires special processes. | Strong impact conditions: Crushers processing materials containing large pieces of metal, stones, and other impurities (scrap cars, bulky waste); impact-resistant parts of mining and metallurgical equipment. |
Stainless Steel | 304, 316, Duplex Steel 2205, Wear-resistant steel such as AR400F | Good corrosion resistance: Suitable for humid, acidic, alkaline, or food-grade environments; some grades also have wear resistance. | Wear resistance is usually lower than dedicated wear-resistant steel; high cost; strength/hardness may not be as good as wear-resistant steel. | Food, pharmaceutical, and chemical corrosive environments: Food conveying, chemical raw material processing, wastewater treatment equipment blades. |
Carbon Steel/Low-Alloy Steel + Surface Hardening | Q235B, Q345B + Overlay Welding/Spraying Wear-Resistant Layer | Economical and flexible: Low base material cost; wear-resistant layer can be customized as needed (hardness, thickness, location); can be repaired after wear. | Wear-resistant layer may peel off; complex process, quality depends on technology; overall performance is not as good as integral wear-resistant materials. | Areas with severe localized wear; limited budget but need to improve wear resistance; repairing old blades. Commonly used welding materials: Tungsten carbide composites, high-chromium cast iron welding materials. |
Engineering Plastics/Composite Materials | Ultra-High Molecular Weight Polyethylene (UHMWPE), Nylon (PA), Reinforced Composite Materials | Light weight; corrosion resistance; self-lubricating (not easy to stick to materials); low operating noise. |
Previous article : How to Choose Screw Flighting: Key is Evaluating the Application Scenario
Next article : Spiral Blade: Core Considerations for Material Selection
Similar products
MoreMachining Process Analysis of Carbon Steel Fixed Anchor Plates
- Process : Machining - CNC milling or milling machining
- Material : Carbon steel
Cone Crusher Mantle
- Process : -
- Material :
What are the machining processes used for processing axial fan housings
- Process : Sheet metal - Welding
- Material : Carbon steel
Custom Fabrication of S355JR Welded H-Beams for Construction Projects
- Process : Sheet metal - Welding
- Material : Carbon steel
Drill Stabilizers Applied in Oil Drilling Platforms
- Process : Machining - Five-axis machining
- Material : Alloy steel
Precision Machining of U-Steel Profiles for Building Applications
- Process : Stamping - General stamping
- Material : Aluminum
Heavy-Walled Flange Milling-Turning Machining and Flaw Detection
- Process : Machining - Turning Milling compound
- Material : Alloy steel
Innovative skiving technology: Breaking through the bottleneck of high-density heat dissipation technology
- Process : Surface treatment - Others
- Material : Alloy steel
More products
MoreMachining Process Analysis of Carbon Steel Fixed Anchor Plates
- Process : Machining - CNC milling or milling machining
- Material : Carbon steel
Cone Crusher Mantle
- Process : -
- Material :
What are the machining processes used for processing axial fan housings
- Process : Sheet metal - Welding
- Material : Carbon steel
Custom Fabrication of S355JR Welded H-Beams for Construction Projects
- Process : Sheet metal - Welding
- Material : Carbon steel
Drill Stabilizers Applied in Oil Drilling Platforms
- Process : Machining - Five-axis machining
- Material : Alloy steel
Precision Machining of U-Steel Profiles for Building Applications
- Process : Stamping - General stamping
- Material : Aluminum
Heavy-Walled Flange Milling-Turning Machining and Flaw Detection
- Process : Machining - Turning Milling compound
- Material : Alloy steel
Innovative skiving technology: Breaking through the bottleneck of high-density heat dissipation technology
- Process : Surface treatment - Others
- Material : Alloy steel