What Role Does the Superheater Play in the Steam Boiler Industry
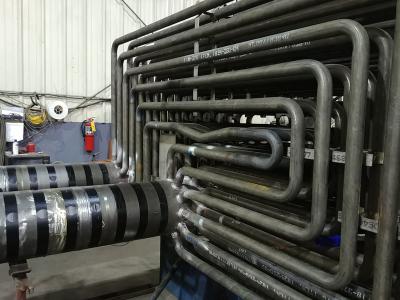
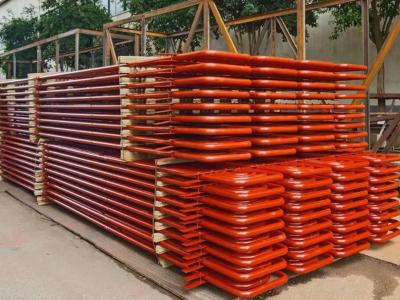
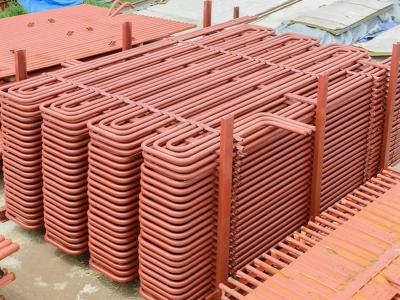
Product name: | What Role Does the Superheater Play in the Steam Boiler Industry |
Keywords: | Boiler Superheater, Function of Boiler Superheater, Impact of Superheater on Boiler, Superheater Structure, Superheater Processing Methods |
Industry: | Mechanical and electrical - Boiler industry |
Process: | Sheet metal - Bending |
Material: | Alloy steel |
Processing manufacturer
- There are 56 manufacturers that provide similar products
- There are 192 manufacturers that provide this processing technology
- There are 64 manufacturers that provide this material processing service
- There are 145 manufacturers that provide this industry processing service
Product details
The superheater plays a crucial role in the industrial boiler industry, and its function and impact are directly related to the boilers performance, efficiency, and operational reliability. The following are the main functions and impacts of superheaters in industrial boilers:
Superheated steam has a higher enthalpy and is suitable for driving steam turbines for power generation or meeting high-temperature process requirements (such as in the chemical and paper industries).
Superheated steam reduces condensation losses in turbines or process equipment, increasing the energy utilization rate of the entire system.
Superheated steam has high dryness, reducing liquid water corrosion or impact in pipelines and equipment, improving system safety.
Depending on the boiler design, the superheater can be divided into radiant, convective, or combined types, flexibly adapting to different operating conditions.
If the superheater is poorly designed (e.g., insufficient heat transfer area or scaling inside the tubes), it can lead to insufficient steam temperature, reduce system efficiency, and increase fuel costs.
Superheater tube bundles may face high-temperature creep, oxidation, corrosion, or wear, and failure (such as tube rupture) can lead to boiler shutdown or safety accidents.
However, if the superheater accumulates ash or becomes blocked, it may increase flue gas resistance, affect combustion efficiency, and thus increase pollutant emissions.
Regular inspection of ash accumulation, wear, and corrosion is required during operation, and maintenance costs are high, especially in coal-fired or waste incineration boilers.
Stable superheater operation helps to extend the service life of downstream equipment and reduce maintenance frequency.
Functions
Increase Steam Temperature:
The superheater heats saturated steam to a superheated state (above the saturation temperature), significantly increasing the steams temperature and energy content.Superheated steam has a higher enthalpy and is suitable for driving steam turbines for power generation or meeting high-temperature process requirements (such as in the chemical and paper industries).
Improve Boiler Thermal Efficiency:
By absorbing waste heat from flue gas, the superheater improves the thermodynamic efficiency of steam, reduces fuel consumption, and lowers boiler operating costs.Superheated steam reduces condensation losses in turbines or process equipment, increasing the energy utilization rate of the entire system.
Ensure System Performance:
The superheater ensures that the steam reaches the design temperature and pressure, meeting the operating conditions of downstream equipment (such as turbines and heat exchangers).Superheated steam has high dryness, reducing liquid water corrosion or impact in pipelines and equipment, improving system safety.
Optimize Heat Distribution:
The superheater is usually arranged in the high-temperature flue gas area of the boiler and works in coordination with water-cooled walls, convection tube bundles, and other heating surfaces to optimize the distribution and utilization of flue gas heat.Depending on the boiler design, the superheater can be divided into radiant, convective, or combined types, flexibly adapting to different operating conditions.
Impacts
Boiler Efficiency and Economy:
The heat transfer performance of the superheater directly affects the overall thermal efficiency of the boiler. An efficient superheater design can reduce exhaust gas temperature and reduce heat loss.If the superheater is poorly designed (e.g., insufficient heat transfer area or scaling inside the tubes), it can lead to insufficient steam temperature, reduce system efficiency, and increase fuel costs.
Operational Safety:
The superheater is exposed to high temperatures, high pressures, and corrosive flue gas for a long time, and the material and manufacturing quality directly affect its reliability.Superheater tube bundles may face high-temperature creep, oxidation, corrosion, or wear, and failure (such as tube rupture) can lead to boiler shutdown or safety accidents.
Environmental Performance:
By fully utilizing high-temperature flue gas, the superheater reduces exhaust gas temperature, indirectly reducing greenhouse gas emissions and thermal pollution.However, if the superheater accumulates ash or becomes blocked, it may increase flue gas resistance, affect combustion efficiency, and thus increase pollutant emissions.
System Complexity and Maintenance:
The design and arrangement of the superheater increase the complexity of the boiler structure, requiring precise control of steam temperature (e.g., through water spray desuperheating devices) to avoid overheating or overcooling.Regular inspection of ash accumulation, wear, and corrosion is required during operation, and maintenance costs are high, especially in coal-fired or waste incineration boilers.
Impact on Downstream Equipment:
The steam temperature and quality provided by the superheater directly affect the performance of turbines or process equipment. Too high a steam temperature may cause equipment overheating damage, while too low a temperature reduces efficiency.Stable superheater operation helps to extend the service life of downstream equipment and reduce maintenance frequency.
Previous article : How to Properly Choose Convection Tube Bundle Material
Next article : A Brief Analysis of Boiler Furnace Manufacturing Processes
Similar products
MoreMachining Process Analysis of Carbon Steel Fixed Anchor Plates
- Process : Machining - CNC milling or milling machining
- Material : Carbon steel
Heavy-Walled Flange Milling-Turning Machining and Flaw Detection
- Process : Machining - Turning Milling compound
- Material : Alloy steel
Precision Machining of U-Steel Profiles for Building Applications
- Process : Stamping - General stamping
- Material : Aluminum
What are the machining processes used for processing axial fan housings
- Process : Sheet metal - Welding
- Material : Carbon steel
Cone Crusher Mantle
- Process : -
- Material :
Custom Fabrication of S355JR Welded H-Beams for Construction Projects
- Process : Sheet metal - Welding
- Material : Carbon steel
Innovative skiving technology: Breaking through the bottleneck of high-density heat dissipation technology
- Process : Surface treatment - Others
- Material : Alloy steel
Drill Stabilizers Applied in Oil Drilling Platforms
- Process : Machining - Five-axis machining
- Material : Alloy steel
More products
MoreMachining Process Analysis of Carbon Steel Fixed Anchor Plates
- Process : Machining - CNC milling or milling machining
- Material : Carbon steel
Heavy-Walled Flange Milling-Turning Machining and Flaw Detection
- Process : Machining - Turning Milling compound
- Material : Alloy steel
Precision Machining of U-Steel Profiles for Building Applications
- Process : Stamping - General stamping
- Material : Aluminum
What are the machining processes used for processing axial fan housings
- Process : Sheet metal - Welding
- Material : Carbon steel
Cone Crusher Mantle
- Process : -
- Material :
Custom Fabrication of S355JR Welded H-Beams for Construction Projects
- Process : Sheet metal - Welding
- Material : Carbon steel
Innovative skiving technology: Breaking through the bottleneck of high-density heat dissipation technology
- Process : Surface treatment - Others
- Material : Alloy steel
Drill Stabilizers Applied in Oil Drilling Platforms
- Process : Machining - Five-axis machining
- Material : Alloy steel