How to Properly Choose Convection Tube Bundle Material
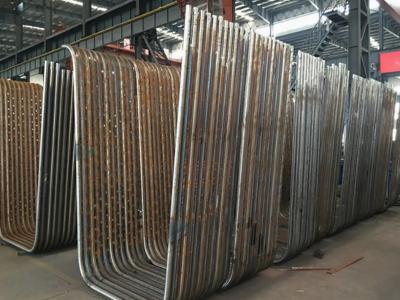
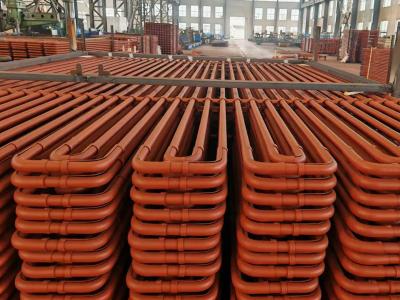
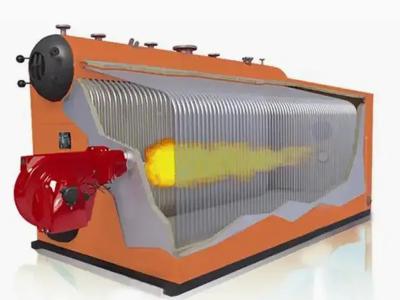
Product name: | How to Properly Choose Convection Tube Bundle Material |
Keywords: | Convection tube bundle material, convection tube bundle process requirements, convection tube bundle reference standards and specifications, convection tube bundle manufacturers |
Industry: | Mechanical and electrical - Boiler industry |
Process: | Machining - CNC milling or milling machining |
Material: | Alloy steel |
Processing manufacturer
- There are 31 manufacturers that provide similar products
- There are 188 manufacturers that provide this processing technology
- There are 109 manufacturers that provide this material processing service
- There are 166 manufacturers that provide this industry processing service
Product details
Properly selecting the material for convection tube bundles requires comprehensive consideration of the boilers operating conditions, operating environment, economics, and manufacturing process requirements. The following are the key steps and factors in selecting convection tube bundle materials:
1. Understand Operating Conditions
Temperature: Convection tube bundles are typically in a medium to high-temperature flue gas environment (approximately 300-800°C, depending on the boiler type and tube bundle location). It is necessary to select a material that can withstand this temperature range to avoid high-temperature creep or strength degradation.
Pressure: The pressure of the working medium inside the tube (such as water or steam) (low pressure, medium pressure, or ultra-high pressure) determines the strength requirements of the material. High-pressure boilers require the use of higher-strength materials.
Circulation Method: Natural circulation, forced circulation, or once-through boilers have different requirements for the materials fatigue resistance.
2. Consider the Flue Gas Environment
Corrosivity: The flue gas may contain sulfides, chlorides, or oxides, which can lead to high-temperature corrosion or low-temperature dew point corrosion. It is necessary to select corrosion-resistant materials, such as low-alloy steel or stainless steel.
Wear: Fly ash from coal-fired boilers can cause tube bundle wear, especially in high-velocity flue gas areas. Materials with high hardness or surface hardening treatment should be selected.
Ash Deposition: Some fuels (such as high-ash coal) are prone to ash deposition, which affects heat transfer efficiency. The surface characteristics of the material (such as smoothness) or additional protective measures (such as fin design) need to be considered.
3. Common Material Selection
Based on the boiler type and operating conditions, the following are commonly used materials for convection tube bundles:
Carbon Steel (e.g., 20# steel, SA-106B):
Suitable for low-pressure, low-temperature boilers (such as small industrial boilers).
Advantages: Low cost, good processing performance.
Disadvantages: Limited high-temperature and corrosion resistance, suitable for flue gas temperatures below 400°C.
Low-Alloy Steel (e.g., 15CrMo, 12Cr1MoV, SA-213 T11/T22):
Suitable for medium-pressure and high-pressure boilers with flue gas temperatures between 400-600°C.
Advantages: Good high-temperature strength and oxidation resistance, high cost-effectiveness.
Disadvantages: Sensitive to high-temperature corrosion, flue gas composition needs to be controlled.
High-Alloy Steel/Stainless Steel (e.g., SA-213 TP304, TP321, TP347):
Suitable for ultra-high pressure, supercritical boilers, or highly corrosive environments (such as waste incineration boilers).
Advantages: Excellent high-temperature corrosion and oxidation resistance, suitable for flue gas temperatures above 600°C.
Disadvantages: High cost, difficult to process.
Wear-Resistant and Corrosion-Resistant Composite Materials:
In high-wear areas, composite tubes with surface overlay welding (such as nickel-based alloys) or sprayed ceramic coatings can be used.
Advantages: Extends service life, reduces maintenance.
Disadvantages: High manufacturing cost.
4. Balance Economics and Performance
Initial Cost: Carbon steel has the lowest cost, while alloy steel and stainless steel have progressively higher costs. Selection should be based on budget and expected lifespan.
Operating and Maintenance Costs: Corrosion-resistant and wear-resistant materials can reduce downtime for maintenance and reduce long-term maintenance costs.
Lifespan Expectation: High-pressure or high-temperature boilers should prioritize high-performance materials to ensure long-term safe operation, while low-pressure boilers can appropriately choose economical materials.
5. Consider Manufacturing and Processing Performance
Weldability: Convection tube bundles need to be welded to headers or tube sheets, so the weldability of the material (such as weld strength, crack tendency) is crucial. Low-alloy steel and carbon steel have good weldability, while high-alloy steel requires special welding processes.
Bending Performance: Convection tube bundles often need to be bent into shape, so the material needs to have good plasticity and toughness to avoid bending cracks.
Heat Treatment Requirements: Some alloy steels require heat treatment (such as normalizing, tempering) to improve performance, so the complexity of the manufacturing process needs to be evaluated.
6. Refer to Standards and Specifications
Follow relevant industry standards, such as:
China: GB/T 5310 (Seamless steel tubes for high-pressure boilers), GB/T 3087 (Seamless steel tubes for low and medium-pressure boilers).
International: ASME SA-213 (Seamless Ferritic and Austenitic Alloy-Steel Boiler, Superheater, and Heat-Exchanger Tubes), ASTM A106 (Seamless Carbon Steel Pipe for High-Temperature Service).
Based on the boiler design parameters, refer to the materials recommended by the standards and ensure that the materials meet certification requirements.
7. Combine Practical Application Experience
Fuel Type: The flue gas composition of coal-fired, oil-fired, natural gas, or biomass boilers varies greatly. For example, oil-fired boilers require materials that are more resistant to sulfur corrosion.
Operating Condition Changes: Consider whether the boiler frequently starts and stops (requires thermal fatigue resistance) or has fluctuating operating loads (requires creep resistance).
Historical Data: Refer to the operating records of similar boilers to understand the performance and failure modes of common materials and optimize the selection.
8. Additional Protective Measures
If the material itself is difficult to fully meet the requirements, performance can be enhanced by:
Surface Treatment: Such as spraying wear-resistant and corrosion-resistant coatings, nitriding, or roller burnishing.
Structural Optimization: Adding wear-resistant sleeves, fins, or turbulence-inducing elements to reduce wear and ash deposition.
Operational Optimization: Reducing corrosion and wear of the material by controlling flue gas velocity or regularly soot blowing.
1. Understand Operating Conditions
Temperature: Convection tube bundles are typically in a medium to high-temperature flue gas environment (approximately 300-800°C, depending on the boiler type and tube bundle location). It is necessary to select a material that can withstand this temperature range to avoid high-temperature creep or strength degradation.
Pressure: The pressure of the working medium inside the tube (such as water or steam) (low pressure, medium pressure, or ultra-high pressure) determines the strength requirements of the material. High-pressure boilers require the use of higher-strength materials.
Circulation Method: Natural circulation, forced circulation, or once-through boilers have different requirements for the materials fatigue resistance.
2. Consider the Flue Gas Environment
Corrosivity: The flue gas may contain sulfides, chlorides, or oxides, which can lead to high-temperature corrosion or low-temperature dew point corrosion. It is necessary to select corrosion-resistant materials, such as low-alloy steel or stainless steel.
Wear: Fly ash from coal-fired boilers can cause tube bundle wear, especially in high-velocity flue gas areas. Materials with high hardness or surface hardening treatment should be selected.
Ash Deposition: Some fuels (such as high-ash coal) are prone to ash deposition, which affects heat transfer efficiency. The surface characteristics of the material (such as smoothness) or additional protective measures (such as fin design) need to be considered.
3. Common Material Selection
Based on the boiler type and operating conditions, the following are commonly used materials for convection tube bundles:
Carbon Steel (e.g., 20# steel, SA-106B):
Suitable for low-pressure, low-temperature boilers (such as small industrial boilers).
Advantages: Low cost, good processing performance.
Disadvantages: Limited high-temperature and corrosion resistance, suitable for flue gas temperatures below 400°C.
Low-Alloy Steel (e.g., 15CrMo, 12Cr1MoV, SA-213 T11/T22):
Suitable for medium-pressure and high-pressure boilers with flue gas temperatures between 400-600°C.
Advantages: Good high-temperature strength and oxidation resistance, high cost-effectiveness.
Disadvantages: Sensitive to high-temperature corrosion, flue gas composition needs to be controlled.
High-Alloy Steel/Stainless Steel (e.g., SA-213 TP304, TP321, TP347):
Suitable for ultra-high pressure, supercritical boilers, or highly corrosive environments (such as waste incineration boilers).
Advantages: Excellent high-temperature corrosion and oxidation resistance, suitable for flue gas temperatures above 600°C.
Disadvantages: High cost, difficult to process.
Wear-Resistant and Corrosion-Resistant Composite Materials:
In high-wear areas, composite tubes with surface overlay welding (such as nickel-based alloys) or sprayed ceramic coatings can be used.
Advantages: Extends service life, reduces maintenance.
Disadvantages: High manufacturing cost.
4. Balance Economics and Performance
Initial Cost: Carbon steel has the lowest cost, while alloy steel and stainless steel have progressively higher costs. Selection should be based on budget and expected lifespan.
Operating and Maintenance Costs: Corrosion-resistant and wear-resistant materials can reduce downtime for maintenance and reduce long-term maintenance costs.
Lifespan Expectation: High-pressure or high-temperature boilers should prioritize high-performance materials to ensure long-term safe operation, while low-pressure boilers can appropriately choose economical materials.
5. Consider Manufacturing and Processing Performance
Weldability: Convection tube bundles need to be welded to headers or tube sheets, so the weldability of the material (such as weld strength, crack tendency) is crucial. Low-alloy steel and carbon steel have good weldability, while high-alloy steel requires special welding processes.
Bending Performance: Convection tube bundles often need to be bent into shape, so the material needs to have good plasticity and toughness to avoid bending cracks.
Heat Treatment Requirements: Some alloy steels require heat treatment (such as normalizing, tempering) to improve performance, so the complexity of the manufacturing process needs to be evaluated.
6. Refer to Standards and Specifications
Follow relevant industry standards, such as:
China: GB/T 5310 (Seamless steel tubes for high-pressure boilers), GB/T 3087 (Seamless steel tubes for low and medium-pressure boilers).
International: ASME SA-213 (Seamless Ferritic and Austenitic Alloy-Steel Boiler, Superheater, and Heat-Exchanger Tubes), ASTM A106 (Seamless Carbon Steel Pipe for High-Temperature Service).
Based on the boiler design parameters, refer to the materials recommended by the standards and ensure that the materials meet certification requirements.
7. Combine Practical Application Experience
Fuel Type: The flue gas composition of coal-fired, oil-fired, natural gas, or biomass boilers varies greatly. For example, oil-fired boilers require materials that are more resistant to sulfur corrosion.
Operating Condition Changes: Consider whether the boiler frequently starts and stops (requires thermal fatigue resistance) or has fluctuating operating loads (requires creep resistance).
Historical Data: Refer to the operating records of similar boilers to understand the performance and failure modes of common materials and optimize the selection.
8. Additional Protective Measures
If the material itself is difficult to fully meet the requirements, performance can be enhanced by:
Surface Treatment: Such as spraying wear-resistant and corrosion-resistant coatings, nitriding, or roller burnishing.
Structural Optimization: Adding wear-resistant sleeves, fins, or turbulence-inducing elements to reduce wear and ash deposition.
Operational Optimization: Reducing corrosion and wear of the material by controlling flue gas velocity or regularly soot blowing.
Previous article : Large Tube Sheet Forging Process
Similar products
MoreMachining Process Analysis of Carbon Steel Fixed Anchor Plates
- Process : Machining - CNC milling or milling machining
- Material : Carbon steel
What are the machining processes used for processing axial fan housings
- Process : Sheet metal - Welding
- Material : Carbon steel
Heavy-Walled Flange Milling-Turning Machining and Flaw Detection
- Process : Machining - Turning Milling compound
- Material : Alloy steel
Precision Machining of U-Steel Profiles for Building Applications
- Process : Stamping - General stamping
- Material : Aluminum
Cone Crusher Mantle
- Process : -
- Material :
Innovative skiving technology: Breaking through the bottleneck of high-density heat dissipation technology
- Process : Surface treatment - Others
- Material : Alloy steel
Custom Fabrication of S355JR Welded H-Beams for Construction Projects
- Process : Sheet metal - Welding
- Material : Carbon steel
Drill Stabilizers Applied in Oil Drilling Platforms
- Process : Machining - Five-axis machining
- Material : Alloy steel
More products
MoreMachining Process Analysis of Carbon Steel Fixed Anchor Plates
- Process : Machining - CNC milling or milling machining
- Material : Carbon steel
What are the machining processes used for processing axial fan housings
- Process : Sheet metal - Welding
- Material : Carbon steel
Heavy-Walled Flange Milling-Turning Machining and Flaw Detection
- Process : Machining - Turning Milling compound
- Material : Alloy steel
Precision Machining of U-Steel Profiles for Building Applications
- Process : Stamping - General stamping
- Material : Aluminum
Cone Crusher Mantle
- Process : -
- Material :
Innovative skiving technology: Breaking through the bottleneck of high-density heat dissipation technology
- Process : Surface treatment - Others
- Material : Alloy steel
Custom Fabrication of S355JR Welded H-Beams for Construction Projects
- Process : Sheet metal - Welding
- Material : Carbon steel
Drill Stabilizers Applied in Oil Drilling Platforms
- Process : Machining - Five-axis machining
- Material : Alloy steel