What is a Rigid Centralizer?
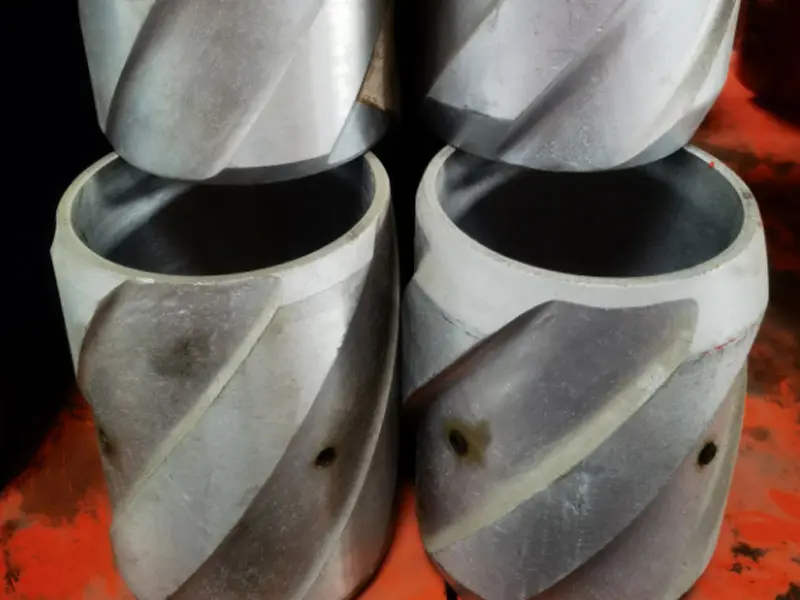
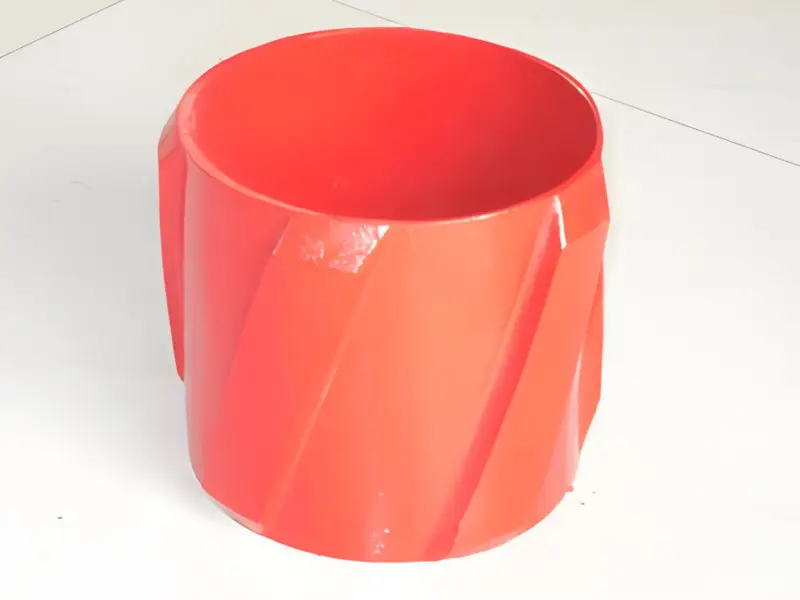
Product name: | What is a Rigid Centralizer? |
Keywords: | Rigid Centralizer |
Industry: | Petroleum, natural gas and chemical industry - Petroleum and natural gas industry |
Process: | Casting - Precision casting |
Material: | Alloy steel |
Processing manufacturer
- There are 56 manufacturers that provide similar products
- There are 136 manufacturers that provide this processing technology
- There are 104 manufacturers that provide this material processing service
- There are 110 manufacturers that provide this industry processing service
Product details
A rigid centralizer is a device used in oil drilling or production operations, primarily to ensure the central position of casing or sucker rods in the wellbore, preventing wear and improving cementation quality. Unlike flexible centralizers (such as bow spring centralizers), it has a fixed structure and no elastic deformation capability, making it suitable for specific well conditions.
Features of Rigid Centralizers
- Structure:
- Made of sturdy materials such as cast iron, cast aluminum, steel, or high-strength composite materials.
- Typically designed as one-piece or split-piece, with surfaces that may have straight ribs, helical ribs, or roller structures.
- Has no elastic restoring force, relying on a fixed shape and rigid support to keep the casing centered.
- Function:
- Centralizing Casing: Ensures the casing is centered in the wellbore, forming a uniform cement sheath and improving cementation quality.
- Reducing Friction: Some rigid centralizers (such as roller types) reduce frictional resistance during casing running through roller designs, suitable for deviated or horizontal wells.
- Preventing Wear: In complex well conditions, prevents direct contact between the casing or sucker rods and the wellbore wall, reducing wear.
- Applicable Scenarios:
- Deviated and Horizontal Wells: Rigid centralizers are suitable for complex wellbore trajectories due to their high strength and stability.
- Irregular Wellbore Diameters: Helical rigid centralizers can improve cement slurry displacement efficiency through swirling flow.
- High-Temperature and High-Pressure Wells: High-temperature and corrosion-resistant materials make them suitable for harsh environments.
Common Types
- Straight-Rib Rigid Centralizer: Simple structure, suitable for vertical or moderately complex well conditions.
- Helical Rigid Centralizer: With helical blades, improves cement slurry flow during cementation, suitable for irregular wellbores.
- Roller Rigid Centralizer: With rollers on the surface, reduces frictional resistance, commonly used for long casing runs (such as Panjin Kaisheng Petroleum Machinerys rolling centralizers).
Differences from Flexible Centralizers
- Rigid Centralizer: Fixed shape, no elastic deformation, suitable for well conditions requiring high strength, may have a higher coefficient of friction.
- Flexible Centralizer: Such as bow spring type, has elastic restoring force, suitable for vertical or moderately complex well conditions, flexible installation but lower strength.
Selection Considerations
- Well Condition Matching: Select the model according to wellbore trajectory, casing size, and frictional resistance requirements (such as 5-1/2" or 7" casing).
- Material Durability: Ensure the material is corrosion-resistant and high-temperature resistant to avoid breakage (such as the centralizer breakage problem mentioned in the Graff project).
- Installation Spacing: Design reasonable spacing according to API standards or oilfield experience (usually one every 10-15 meters).
Previous article : Corrosion-Resistant High-Precision Stainless Steel Rings
Next article : Open Hole Packers in the Oil Industry
Similar products
MoreMachining Process Analysis of Carbon Steel Fixed Anchor Plates
- Process : Machining - CNC milling or milling machining
- Material : Carbon steel
Cone Crusher Mantle
- Process : -
- Material :
What are the machining processes used for processing axial fan housings
- Process : Sheet metal - Welding
- Material : Carbon steel
Custom Fabrication of S355JR Welded H-Beams for Construction Projects
- Process : Sheet metal - Welding
- Material : Carbon steel
Drill Stabilizers Applied in Oil Drilling Platforms
- Process : Machining - Five-axis machining
- Material : Alloy steel
Precision Machining of U-Steel Profiles for Building Applications
- Process : Stamping - General stamping
- Material : Aluminum
Heavy-Walled Flange Milling-Turning Machining and Flaw Detection
- Process : Machining - Turning Milling compound
- Material : Alloy steel
Innovative skiving technology: Breaking through the bottleneck of high-density heat dissipation technology
- Process : Surface treatment - Others
- Material : Alloy steel
More products
MoreMachining Process Analysis of Carbon Steel Fixed Anchor Plates
- Process : Machining - CNC milling or milling machining
- Material : Carbon steel
Cone Crusher Mantle
- Process : -
- Material :
What are the machining processes used for processing axial fan housings
- Process : Sheet metal - Welding
- Material : Carbon steel
Custom Fabrication of S355JR Welded H-Beams for Construction Projects
- Process : Sheet metal - Welding
- Material : Carbon steel
Drill Stabilizers Applied in Oil Drilling Platforms
- Process : Machining - Five-axis machining
- Material : Alloy steel
Precision Machining of U-Steel Profiles for Building Applications
- Process : Stamping - General stamping
- Material : Aluminum
Heavy-Walled Flange Milling-Turning Machining and Flaw Detection
- Process : Machining - Turning Milling compound
- Material : Alloy steel
Innovative skiving technology: Breaking through the bottleneck of high-density heat dissipation technology
- Process : Surface treatment - Others
- Material : Alloy steel