Open Hole Packers in the Oil Industry
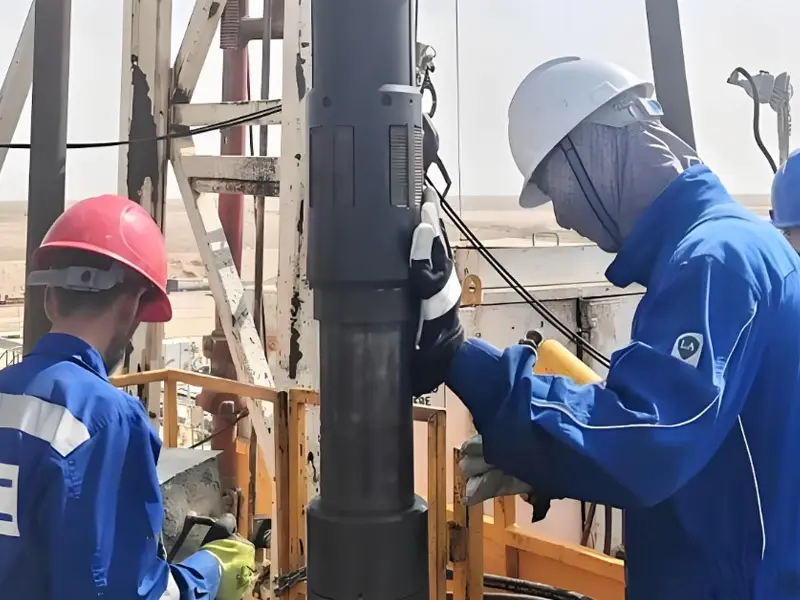
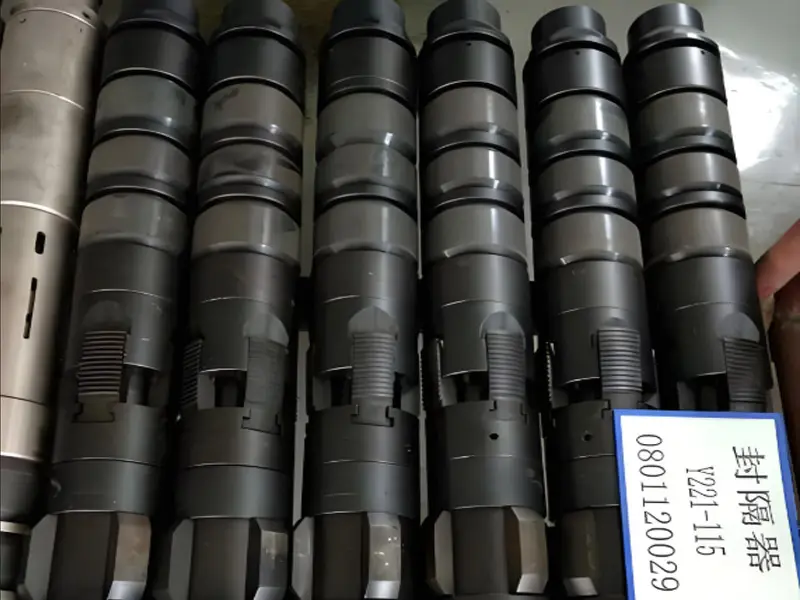
Product name: | Open Hole Packers in the Oil Industry |
Keywords: | Open Hole Packers |
Industry: | Petroleum, natural gas and chemical industry - Petroleum and natural gas industry |
Process: | Machining - CNC milling or milling machining |
Material: | Alloy steel |
Processing manufacturer
- There are 57 manufacturers that provide similar products
- There are 150 manufacturers that provide this processing technology
- There are 77 manufacturers that provide this material processing service
- There are 174 manufacturers that provide this industry processing service
Product details
Open hole packers are sealing tools used in the oil industry for open hole wells (i.e., well sections without casing). They are primarily used to separate different formations or zones within the wellbore to enable zonal operations, improve recovery rates, or control fluid flow within the well. The following is a detailed description of open hole packers:
Definition of Open Hole Packers
An open hole packer is a specially designed sealing device installed in an open hole section (uncased wellbore) that directly contacts the wellbore wall through expansion or mechanical means to form a seal, isolating different pressure or fluid zones within the well. It is widely used in zonal oil production, fracturing, acidizing, or testing operations.
Main Functions
- Zonal Isolation: Divides the open hole section into multiple independent zones, preventing fluid crossflow between formations (such as oil, water, or gas).
- Supports Zonal Operations: Facilitates precise formation treatment with multi-stage fracturing or zonal water injection.
- Improves Recovery Rate: Optimizes oil and gas production by isolating low-producing or high-water-cut zones.
- Controls Fluid Flow Within the Well: Prevents gas breakthrough or water coning, improving production efficiency.
Types of Open Hole Packers
Based on working principles and application scenarios, open hole packers can be divided into the following types:
- Inflatable Packers:
- Principle: The packers rubber element expands through hydraulic or chemical reactions, tightly adhering to the wellbore wall to form a seal.
- Features: Adapts to irregular wellbore diameters (such as elliptical or irregular wellbores) with good sealing performance.
- Common Materials: High-strength rubber (such as HNBR or FKM) combined with a steel or composite material body.
- Applications: Multi-stage fracturing, complex horizontal wells (such as shale gas development).
- Mechanical Packers:
- Principle: A mechanical device (such as a cone or slider) drives the sealing element to expand and contact the wellbore wall.
- Features: Simple structure, reusable, but requires a high degree of wellbore regularity.
- Applications: Conventional open hole zonal testing or water injection operations.
- Chemical Expansion Packers:
- Principle: Uses water-absorbing and expanding materials (such as polymer) to expand upon contact with water, forming a seal.
- Features: Suitable for long-term sealing, easy to install, but affected by formation fluid properties.
- Applications: Long-term zonal isolation or abandoned well plugging.
- Composite Packers:
- Principle: Combines expansion and mechanical methods, offering both high adaptability and reliability.
- Applications: Deep wells, ultra-deep wells, or high-temperature, high-pressure (HPHT) environments.
Common Materials
- Body: High-strength steel (such as 4140, 4130 low-alloy steel) or corrosion-resistant alloys (such as Inconel) to withstand high-temperature, high-pressure, or corrosive environments.
- Sealing Element: Oil-resistant, high-temperature-resistant rubber materials (such as hydrogenated nitrile rubber HNBR, fluororubber FKM) or expandable polymers.
- Surface Coating: Some packers have wear-resistant or corrosion-resistant coatings (such as tungsten carbide spraying) to extend their lifespan.
Manufacturing Process
The manufacturing process of open hole packers is similar to that of rigid centralizers, but with a greater emphasis on sealing performance and wellbore adaptability:
- Precision Casting/Forging: Manufacturing high-strength bodies to ensure pressure resistance.
- Rubber Molding: Producing sealing elements through molding or extrusion processes to ensure expansion performance and durability.
- Machining: Turning and milling to ensure the precision of the body and sealing elements, meeting wellbore diameter requirements.
- Surface Treatment: Heat treatment to increase body strength, chemical plating or spraying to enhance corrosion resistance.
- Assembly and Testing: Performing sealing performance and pressure resistance tests in high-pressure environments, complying with API or ISO standards (such as API 11D1).
Application Scenarios
- Multi-Stage Fracturing: In the development of shale gas or tight oil and gas reservoirs, open hole packers are used for zonal fracturing (such as in conjunction with sliding sleeve systems).
- Zonal Oil Production: Isolating high-water-cut or low-producing zones to optimize oil and gas recovery.
- Formation Testing: Isolating test sections to obtain accurate formation pressure or fluid data.
- Water Injection Wells: Separating different injection zones to control injection direction and pressure.
- Complex Well Conditions: Inflatable packers are more advantageous in high-temperature, high-pressure wells, horizontal wells, or irregular wellbore diameter wells.
Similar products
MoreMachining Process Analysis of Carbon Steel Fixed Anchor Plates
- Process : Machining - CNC milling or milling machining
- Material : Carbon steel
Cone Crusher Mantle
- Process : -
- Material :
What are the machining processes used for processing axial fan housings
- Process : Sheet metal - Welding
- Material : Carbon steel
Custom Fabrication of S355JR Welded H-Beams for Construction Projects
- Process : Sheet metal - Welding
- Material : Carbon steel
Drill Stabilizers Applied in Oil Drilling Platforms
- Process : Machining - Five-axis machining
- Material : Alloy steel
Precision Machining of U-Steel Profiles for Building Applications
- Process : Stamping - General stamping
- Material : Aluminum
Heavy-Walled Flange Milling-Turning Machining and Flaw Detection
- Process : Machining - Turning Milling compound
- Material : Alloy steel
Innovative skiving technology: Breaking through the bottleneck of high-density heat dissipation technology
- Process : Surface treatment - Others
- Material : Alloy steel
More products
MoreMachining Process Analysis of Carbon Steel Fixed Anchor Plates
- Process : Machining - CNC milling or milling machining
- Material : Carbon steel
Cone Crusher Mantle
- Process : -
- Material :
What are the machining processes used for processing axial fan housings
- Process : Sheet metal - Welding
- Material : Carbon steel
Custom Fabrication of S355JR Welded H-Beams for Construction Projects
- Process : Sheet metal - Welding
- Material : Carbon steel
Drill Stabilizers Applied in Oil Drilling Platforms
- Process : Machining - Five-axis machining
- Material : Alloy steel
Precision Machining of U-Steel Profiles for Building Applications
- Process : Stamping - General stamping
- Material : Aluminum
Heavy-Walled Flange Milling-Turning Machining and Flaw Detection
- Process : Machining - Turning Milling compound
- Material : Alloy steel
Innovative skiving technology: Breaking through the bottleneck of high-density heat dissipation technology
- Process : Surface treatment - Others
- Material : Alloy steel