Manufacturing Process of Lathe Beds
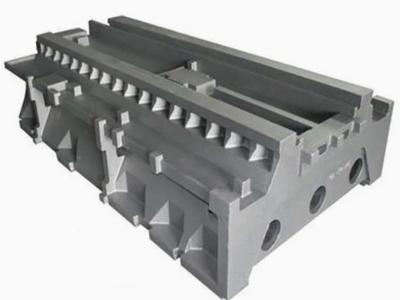
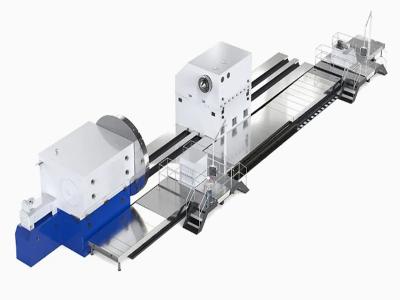
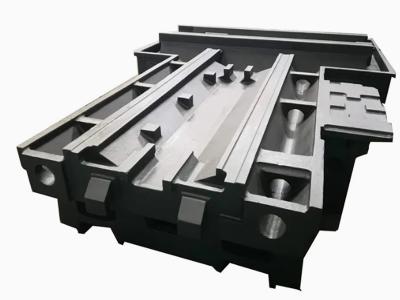
Product name: | Manufacturing Process of Lathe Beds |
Keywords: | Lathe bed manufacturing process, lathe bed casting process, rough machining of lathe beds, lathe bed surface treatment |
Industry: | Mechanical and electrical - Machine tool, machinery and equipment manufacturing industry |
Process: | Casting - Others |
Material: | Hard alloys |
Processing manufacturer
- There are 59 manufacturers that provide similar products
- There are 149 manufacturers that provide this processing technology
- There are 113 manufacturers that provide this material processing service
- There are 137 manufacturers that provide this industry processing service
Product details
The manufacturing process of lathe beds involves multiple steps to ensure the accuracy, strength, and stability of the bed, meeting the high-precision machining requirements of lathes. The following is a summary of the main process flow and key technical points of lathe bed machining, compiled from existing information:
1. Material Selection
- Common Materials: Lathe beds are typically made of high-strength cast iron (such as HT250 or HT300) due to its good vibration resistance, rigidity, and wear resistance. Some high-precision machine tools may use ductile iron or welded steel structures.
- Reason: Cast iron has excellent casting performance and damping capacity, making it suitable for withstanding cutting forces and vibrations; steel structures are used for lightweighting or special design requirements.
2. Casting (or Welding)
- Casting Process:
- Mold Design: Create precision sand molds or metal molds based on the lathe bed design drawings to ensure accurate dimensions and shape of the casting.
- Melting and Pouring: Use a medium-frequency induction furnace to melt the cast iron, controlling the chemical composition (such as carbon and silicon content). Ensure uniform temperature during pouring to prevent defects such as porosity and shrinkage.
- Cooling and Cleaning: After the casting cools, perform sandblasting or shot peening to remove surface sand and scale.
- Welding Process (if using steel structure):
- Cut high-strength steel plates into shape and assemble the bed frame by welding.
- Annealing treatment is required to eliminate welding stress and ensure structural stability.
3. Rough Machining
- Purpose: Remove excess material from the surface of the casting or welded part for initial shaping.
- Equipment: Large gantry milling machines, boring machines, or CNC machining centers.
- Process:
- Datum Surface Machining: Determine the datum surface of the bed (such as the bottom surface or guide rail surface) to ensure positioning accuracy for subsequent machining.
- Milling: Rough mill the main planes of the bed (such as the guide rail mounting surface, bottom surface), leaving a machining allowance (typically 2-5mm).
- Drilling: Machine mounting holes, coolant grooves, and other structures, ensuring hole position accuracy.
4. Heat Treatment
- Aging Treatment:
- Natural Aging: Place the casting for several months to a year, relying on the natural environment to eliminate internal stress. This method is low-cost but has a long cycle time.
- Artificial Aging: Eliminate residual stress through vibration aging or thermal aging (heating to 500-600°C and then slowly cooling) to improve dimensional stability.
- Purpose: Reduce deformation during subsequent machining and use, ensuring long-term stability of the bed.
5. Finish Machining
- Equipment: High-precision CNC gantry milling machines, grinding machines, or guideway grinders.
- Process:
- Guideway Surface Machining: The guideway surface of the lathe bed is a critical part, requiring high flatness and surface finish (Ra0.8-1.6). It is usually precision milled and then ground, or directly processed using a guideway grinder.
- Flatness Control: The flatness error of the guideway surface needs to be controlled within 0.01-0.02mm/m.
- Hole System Finish Machining: Bore or ream the holes for mounting the headstock, tailstock, etc., ensuring coaxiality and positional accuracy.
- Surface Hardening (optional): Harden the guideway surface by high-frequency quenching or apply plastic (such as PTFE guideway soft belt) to improve wear resistance and anti-stick-slip properties.
6. Surface Treatment
- Polishing or Painting: Polish or spray anti-rust paint on non-functional surfaces to improve appearance and corrosion resistance.
- Guideway Lubrication Grooves: Machine lubrication oil grooves or install a lubrication system to ensure long-term smooth operation of the guideways.
7. Inspection and Calibration
- Inspection Equipment: Coordinate measuring machines, laser interferometers, levels, etc.
- Inspection Content:
- Geometric Accuracy: Check the parallelism, flatness, and straightness of the guideway surface.
- Positional Accuracy: Verify the positional tolerance and coaxiality of the hole system.
- Surface Quality: Measure surface roughness and hardness.
- Calibration: If deviations are found, use scraping (manual or mechanical) to make slight corrections to the guideway surface to ensure accuracy.
8. Assembly and Debugging
- Assembly: Install components such as the headstock, tailstock, and tool post onto the bed, and adjust the fitting accuracy of each component.
- Debugging: Perform trial runs to check the vibration, noise, and machining accuracy of the bed, and fine-tune the guideways or re-scrape if necessary.
Key Technical Points
- Cutting Parameter Selection: Select appropriate cutting speed, feed rate, and depth of cut based on the material and machining stage to avoid rapid tool wear or workpiece deformation.
- Accuracy Control: The machining accuracy of the guideway surface directly affects the machining performance of the lathe, so it is necessary to strictly control the flatness and straightness.
- Stress Relief: Heat treatment after casting or welding is a critical step to prevent deformation during long-term use.
- Equipment Selection: Large beds require the use of large-stroke CNC machine tools (such as gantry milling machines) to ensure machining efficiency and accuracy.
Previous article : Centralizer Installation Key Points
Next article : Rotary Steerable Stabilizer
Similar products
MoreMachining Process Analysis of Carbon Steel Fixed Anchor Plates
- Process : Machining - CNC milling or milling machining
- Material : Carbon steel
What are the machining processes used for processing axial fan housings
- Process : Sheet metal - Welding
- Material : Carbon steel
Cone Crusher Mantle
- Process : -
- Material :
Custom Fabrication of S355JR Welded H-Beams for Construction Projects
- Process : Sheet metal - Welding
- Material : Carbon steel
Drill Stabilizers Applied in Oil Drilling Platforms
- Process : Machining - Five-axis machining
- Material : Alloy steel
Heavy-Walled Flange Milling-Turning Machining and Flaw Detection
- Process : Machining - Turning Milling compound
- Material : Alloy steel
Precision Machining of U-Steel Profiles for Building Applications
- Process : Stamping - General stamping
- Material : Aluminum
Innovative skiving technology: Breaking through the bottleneck of high-density heat dissipation technology
- Process : Surface treatment - Others
- Material : Alloy steel
More products
MoreMachining Process Analysis of Carbon Steel Fixed Anchor Plates
- Process : Machining - CNC milling or milling machining
- Material : Carbon steel
What are the machining processes used for processing axial fan housings
- Process : Sheet metal - Welding
- Material : Carbon steel
Cone Crusher Mantle
- Process : -
- Material :
Custom Fabrication of S355JR Welded H-Beams for Construction Projects
- Process : Sheet metal - Welding
- Material : Carbon steel
Drill Stabilizers Applied in Oil Drilling Platforms
- Process : Machining - Five-axis machining
- Material : Alloy steel
Heavy-Walled Flange Milling-Turning Machining and Flaw Detection
- Process : Machining - Turning Milling compound
- Material : Alloy steel
Precision Machining of U-Steel Profiles for Building Applications
- Process : Stamping - General stamping
- Material : Aluminum
Innovative skiving technology: Breaking through the bottleneck of high-density heat dissipation technology
- Process : Surface treatment - Others
- Material : Alloy steel