Detailed Explanation of Screw Flight Types
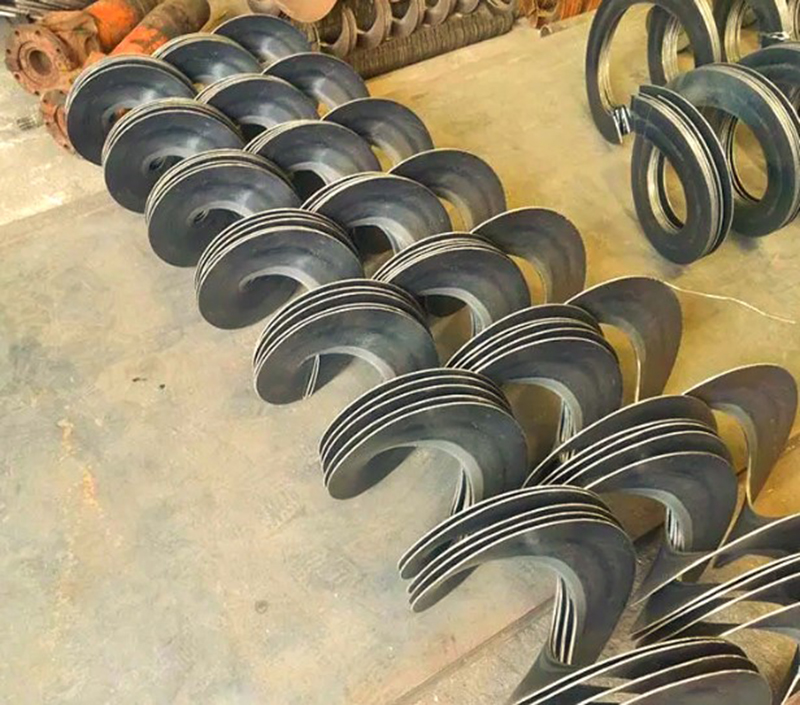
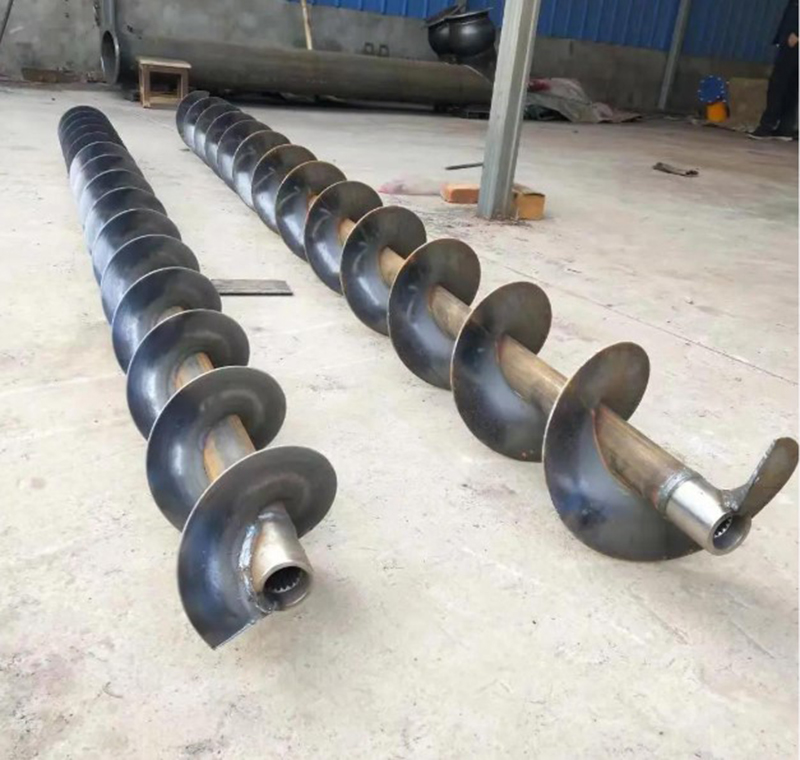

Product name: | Detailed Explanation of Screw Flight Types |
Keywords: | |
Industry: | Metallurgy and minerals - Metallurgy industry |
Process: | - |
Material: |
Processing manufacturer
- There are 48 manufacturers that provide similar products
- There are 167 manufacturers that provide this processing technology
- There are 120 manufacturers that provide this material processing service
- There are 148 manufacturers that provide this industry processing service
Product details
Detailed Explanation of Screw Flight Types
Screw flight types are mainly distinguished based on their structural form, flight continuity, and functional focus:
Solid Flight Screw:
Structure: The most common form, where the flight is a continuous, solid metal strip spiraling around the central axis.
Features: Robust structure, good rigidity, strong thrust, high conveying efficiency, especially suitable for conveying materials with high density and certain friction (such as municipal solid waste, industrial waste, and large materials).
Disadvantages: Relatively heavy, with slightly higher power consumption. May be less flexible than ribbon flights for very fluffy or easily tangled materials.
Ribbon Flight Screw:
Structure: The flight is not solid but consists of one or more continuous metal strips (flat steel or round steel) spirally wound around the central axis, with a large gap between the flight and the shaft.
Features: Lightweight, with relatively low power consumption. Small contact area between the flight and the material, less prone to material sticking or entanglement, especially suitable for handling fluffy, lightweight, easily tangled, and sticky materials (such as waste plastic film, plastic bags, waste paper, crop stalks, and waste textiles).
Disadvantages: Thrust is usually weaker than solid flights, with slightly lower rigidity, and not suitable for conveying excessively heavy or highly abrasive materials.
Paddle Flight Screw:
Structure: Additional paddles (usually flat or angled plates) are welded or installed at intervals on a continuous screw flight.
Features: Combines screw conveying with mixing/breaking functions. The paddles effectively break up lumpy materials, prevent entanglement, and promote material mixing. Suitable for materials with complex compositions, prone to clumping, or requiring pre-mixing.
Disadvantages: Relatively complex structure, with slightly higher manufacturing and maintenance costs.
Variable Pitch Screw:
Structure: The pitch of the screw flight (the spacing between the flights) is not constant, usually gradually decreasing from the feeding end to the discharge end.
Features: Large pitch at the feeding end facilitates rapid reception and conveying of fluffy materials; small pitch at the discharge end increases the compression force on the material, ensuring that the material is tightly and stably pushed into the crushing chamber, improving feeding uniformity and crushing efficiency, and reducing material rebound.
Disadvantages: More complex to design and manufacture than constant pitch flights.
Combination Screw:
Structure: Different types of flights are used in different sections on the same shaft. For example, ribbon or large-pitch flights are used in the feeding section for easy reception and initial conveying, while solid or small-pitch flights are used in the middle or discharge section to enhance thrust and compaction.
Features: Integrates the advantages of different flight types, optimized for material characteristics and crushing process requirements to achieve optimal performance and efficiency.
Disadvantages: The most complex to design and manufacture.
Screw flight types are mainly distinguished based on their structural form, flight continuity, and functional focus:
Solid Flight Screw:
Structure: The most common form, where the flight is a continuous, solid metal strip spiraling around the central axis.
Features: Robust structure, good rigidity, strong thrust, high conveying efficiency, especially suitable for conveying materials with high density and certain friction (such as municipal solid waste, industrial waste, and large materials).
Disadvantages: Relatively heavy, with slightly higher power consumption. May be less flexible than ribbon flights for very fluffy or easily tangled materials.
Ribbon Flight Screw:
Structure: The flight is not solid but consists of one or more continuous metal strips (flat steel or round steel) spirally wound around the central axis, with a large gap between the flight and the shaft.
Features: Lightweight, with relatively low power consumption. Small contact area between the flight and the material, less prone to material sticking or entanglement, especially suitable for handling fluffy, lightweight, easily tangled, and sticky materials (such as waste plastic film, plastic bags, waste paper, crop stalks, and waste textiles).
Disadvantages: Thrust is usually weaker than solid flights, with slightly lower rigidity, and not suitable for conveying excessively heavy or highly abrasive materials.
Paddle Flight Screw:
Structure: Additional paddles (usually flat or angled plates) are welded or installed at intervals on a continuous screw flight.
Features: Combines screw conveying with mixing/breaking functions. The paddles effectively break up lumpy materials, prevent entanglement, and promote material mixing. Suitable for materials with complex compositions, prone to clumping, or requiring pre-mixing.
Disadvantages: Relatively complex structure, with slightly higher manufacturing and maintenance costs.
Variable Pitch Screw:
Structure: The pitch of the screw flight (the spacing between the flights) is not constant, usually gradually decreasing from the feeding end to the discharge end.
Features: Large pitch at the feeding end facilitates rapid reception and conveying of fluffy materials; small pitch at the discharge end increases the compression force on the material, ensuring that the material is tightly and stably pushed into the crushing chamber, improving feeding uniformity and crushing efficiency, and reducing material rebound.
Disadvantages: More complex to design and manufacture than constant pitch flights.
Combination Screw:
Structure: Different types of flights are used in different sections on the same shaft. For example, ribbon or large-pitch flights are used in the feeding section for easy reception and initial conveying, while solid or small-pitch flights are used in the middle or discharge section to enhance thrust and compaction.
Features: Integrates the advantages of different flight types, optimized for material characteristics and crushing process requirements to achieve optimal performance and efficiency.
Disadvantages: The most complex to design and manufacture.
Previous article : Application and Role of Spiral Blades in Crushers
Next article : Detailed Explanation of Screw Blade Materials
Similar products
MoreMachining Process Analysis of Carbon Steel Fixed Anchor Plates
- Process : Machining - CNC milling or milling machining
- Material : Carbon steel
Cone Crusher Mantle
- Process : -
- Material :
What are the machining processes used for processing axial fan housings
- Process : Sheet metal - Welding
- Material : Carbon steel
Custom Fabrication of S355JR Welded H-Beams for Construction Projects
- Process : Sheet metal - Welding
- Material : Carbon steel
Drill Stabilizers Applied in Oil Drilling Platforms
- Process : Machining - Five-axis machining
- Material : Alloy steel
Precision Machining of U-Steel Profiles for Building Applications
- Process : Stamping - General stamping
- Material : Aluminum
Heavy-Walled Flange Milling-Turning Machining and Flaw Detection
- Process : Machining - Turning Milling compound
- Material : Alloy steel
Innovative skiving technology: Breaking through the bottleneck of high-density heat dissipation technology
- Process : Surface treatment - Others
- Material : Alloy steel
More products
MoreMachining Process Analysis of Carbon Steel Fixed Anchor Plates
- Process : Machining - CNC milling or milling machining
- Material : Carbon steel
Cone Crusher Mantle
- Process : -
- Material :
What are the machining processes used for processing axial fan housings
- Process : Sheet metal - Welding
- Material : Carbon steel
Custom Fabrication of S355JR Welded H-Beams for Construction Projects
- Process : Sheet metal - Welding
- Material : Carbon steel
Drill Stabilizers Applied in Oil Drilling Platforms
- Process : Machining - Five-axis machining
- Material : Alloy steel
Precision Machining of U-Steel Profiles for Building Applications
- Process : Stamping - General stamping
- Material : Aluminum
Heavy-Walled Flange Milling-Turning Machining and Flaw Detection
- Process : Machining - Turning Milling compound
- Material : Alloy steel
Innovative skiving technology: Breaking through the bottleneck of high-density heat dissipation technology
- Process : Surface treatment - Others
- Material : Alloy steel