Detailed Explanation of Screw Blade Materials
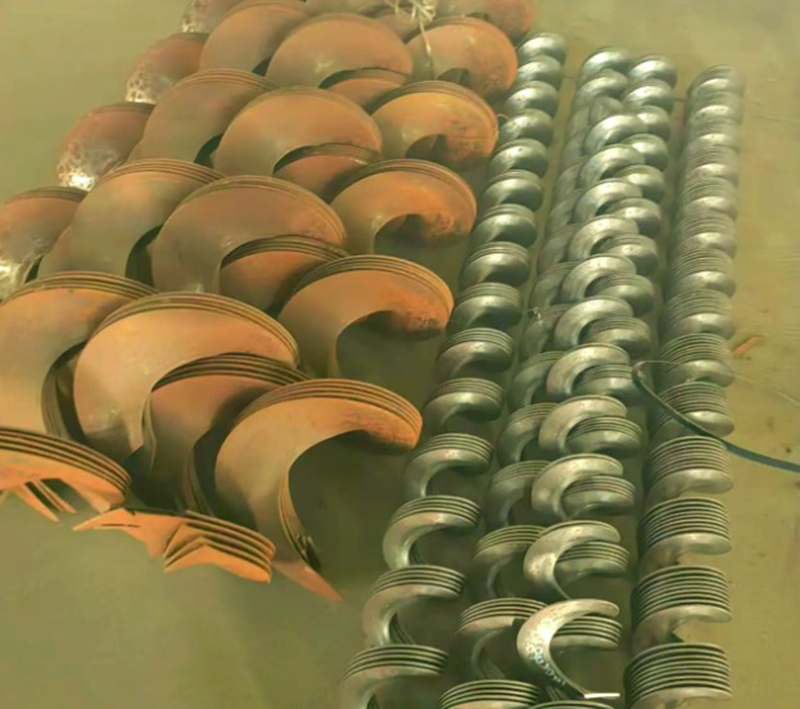
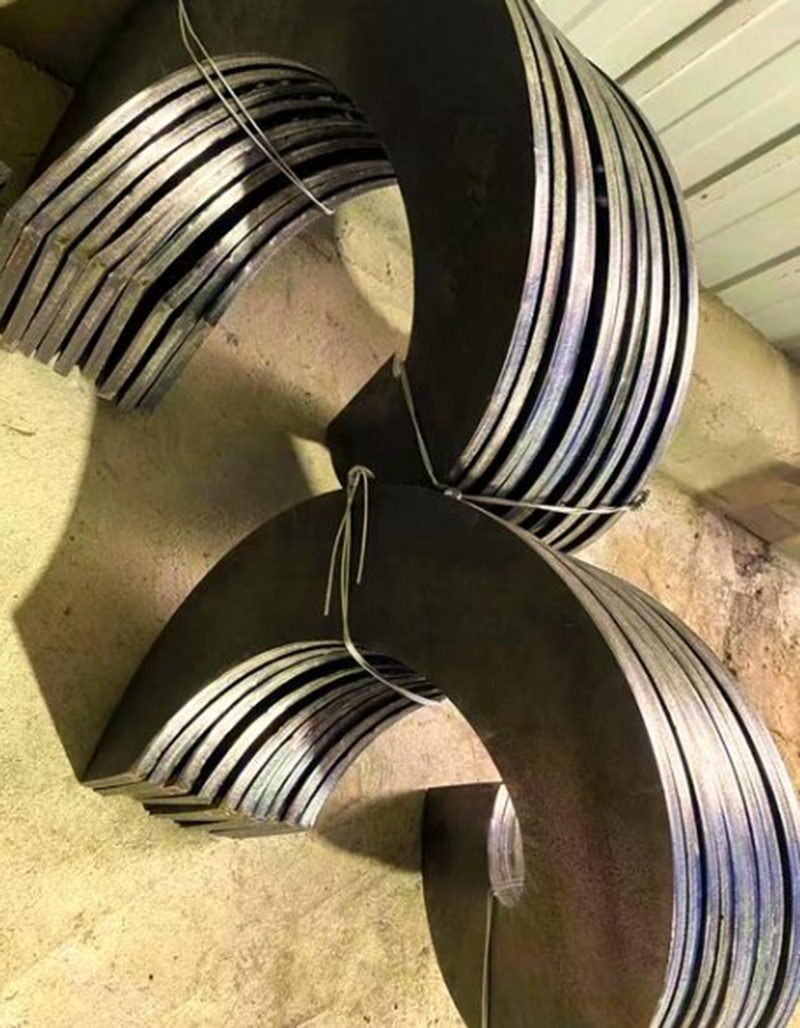
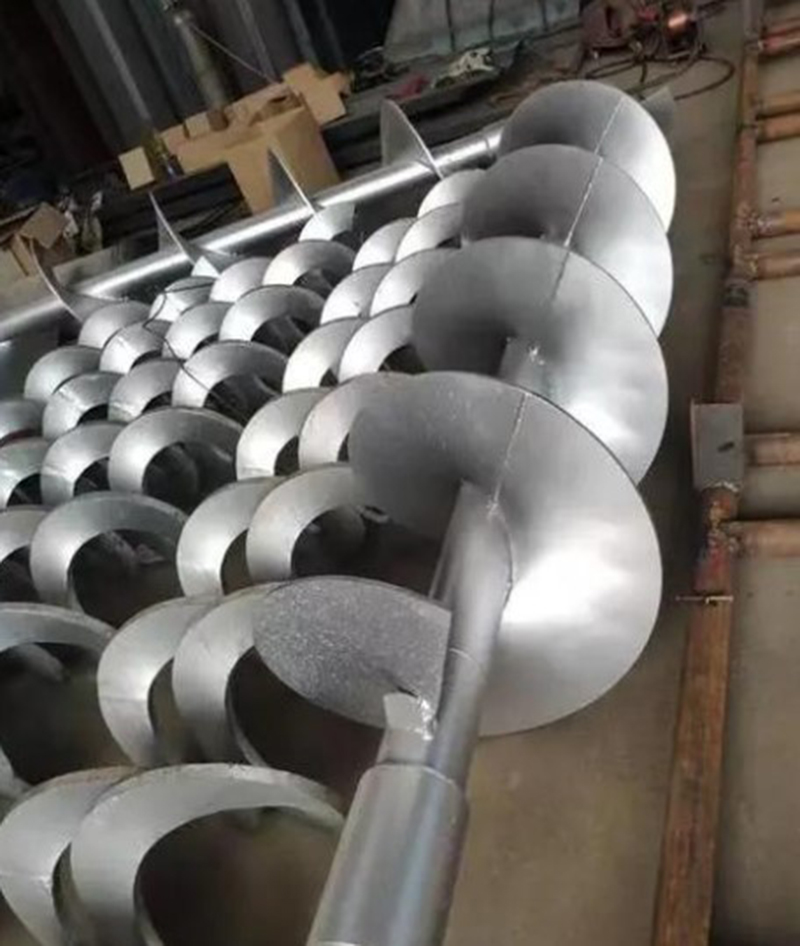
Product name: | Detailed Explanation of Screw Blade Materials |
Keywords: | |
Industry: | Metallurgy and minerals - Metallurgy industry |
Process: | - |
Material: |
Processing manufacturer
- There are 32 manufacturers that provide similar products
- There are 151 manufacturers that provide this processing technology
- There are 61 manufacturers that provide this material processing service
- There are 176 manufacturers that provide this industry processing service
Product details
Screw blades operate in extremely harsh environments: enduring immense torque, intense material friction and wear (abrasive wear, impact wear), potential corrosion (from moisture, acidic or alkaline components in the material), and impact loads. Therefore, material selection is crucial, requiring high strength, high wear resistance, good toughness, and a degree of corrosion resistance. Commonly used materials include:
High-Strength Wear-Resistant Steel Plate (e.g., NM360, NM400, NM450, Hardox 400/450):
Characteristics: This is currently the most widely used material. It achieves high hardness and good wear resistance through heat treatment (quenching + tempering), while maintaining a certain level of toughness and weldability. NM400/NM450/Hardox 450 can reach a hardness of HBW 400-450, providing excellent wear resistance.
Advantages: Good overall performance (strength, hardness, toughness, weldability), cost-effective, and easy to procure and process (cutting, rolling, welding).
Suitable for: The preferred choice for most operating conditions, especially suitable for handling mixed municipal solid waste, industrial waste, construction waste, wood, and other moderately abrasive materials.
High Chromium Cast Iron:
Characteristics: Contains a high proportion of chromium (typically >15%) and carbon, formed through casting. Its wear resistance primarily comes from the large amount of high-hardness carbides (such as M7C3) in the matrix. Hardness can reach HRC 55-65, with extremely high wear resistance, far exceeding that of wear-resistant steel.
Advantages: Top-tier wear resistance, particularly suitable for handling extremely abrasive materials (such as slag, furnace slag, quartz sand, gravel, industrial solid waste containing a large amount of minerals).
Disadvantages: Poor toughness, high brittleness, weak impact resistance, prone to fracture under strong impact; complex casting process, high cost; poor weldability, usually requiring integral casting or connection to the shaft through special methods (such as dovetail grooves, bolts), making maintenance and replacement difficult.
High Manganese Steel (Hadfield Manganese Steel, e.g., Mn13, Mn18):
Characteristics: Typical grade ZGMn13. When subjected to strong impact or extrusion, the surface undergoes significant work hardening, greatly increasing the hardness (surface hardness can reach HBW 500 or higher), thereby achieving excellent impact wear resistance.
Advantages: Extremely good impact toughness, with outstanding wear resistance under strong impact conditions. Suitable for handling materials containing a large amount of large hard objects and metal impurities (such as scrap car shred, bulky waste), capable of withstanding accidental impacts from materials or tools.
Disadvantages: In pure sliding friction conditions without impact or with low impact, the work hardening effect is not obvious, and the wear resistance is not as good as wear-resistant steel or high chromium cast iron; higher cost.
Surface Hardened Steel (e.g., Carbon Steel/Low Alloy Steel + Overlay Welding/Spraying):
Characteristics: Uses a lower-cost base material (such as Q345B) and performs wear-resistant reinforcement treatment on the easily worn parts of the blade (usually the outer edge and propulsion surface).
Overlay Welding (Hardfacing): Melts one or more layers of high-hardness, high-wear-resistant alloy welding material (such as tungsten carbide composite materials, high chromium cast iron welding rods/wires) onto the blade surface. Wear resistance is adjustable and the effect is significant.
Thermal Spraying: Such as arc spraying, flame spraying of tungsten carbide, ceramic, and other wear-resistant coatings.
Advantages: The base material ensures overall strength and toughness, and the wear-resistant layer provides targeted high wear-resistant protection; lower cost compared to using wear-resistant materials throughout; repairable after wear.
Disadvantages: Complex process, high quality control requirements; the overlay welding layer may have cracking or peeling risks; difficult to process for blades with complex shapes.
Similar products
MoreMachining Process Analysis of Carbon Steel Fixed Anchor Plates
- Process : Machining - CNC milling or milling machining
- Material : Carbon steel
Cone Crusher Mantle
- Process : -
- Material :
What are the machining processes used for processing axial fan housings
- Process : Sheet metal - Welding
- Material : Carbon steel
Custom Fabrication of S355JR Welded H-Beams for Construction Projects
- Process : Sheet metal - Welding
- Material : Carbon steel
Drill Stabilizers Applied in Oil Drilling Platforms
- Process : Machining - Five-axis machining
- Material : Alloy steel
Precision Machining of U-Steel Profiles for Building Applications
- Process : Stamping - General stamping
- Material : Aluminum
Heavy-Walled Flange Milling-Turning Machining and Flaw Detection
- Process : Machining - Turning Milling compound
- Material : Alloy steel
Innovative skiving technology: Breaking through the bottleneck of high-density heat dissipation technology
- Process : Surface treatment - Others
- Material : Alloy steel
More products
MoreMachining Process Analysis of Carbon Steel Fixed Anchor Plates
- Process : Machining - CNC milling or milling machining
- Material : Carbon steel
Cone Crusher Mantle
- Process : -
- Material :
What are the machining processes used for processing axial fan housings
- Process : Sheet metal - Welding
- Material : Carbon steel
Custom Fabrication of S355JR Welded H-Beams for Construction Projects
- Process : Sheet metal - Welding
- Material : Carbon steel
Drill Stabilizers Applied in Oil Drilling Platforms
- Process : Machining - Five-axis machining
- Material : Alloy steel
Precision Machining of U-Steel Profiles for Building Applications
- Process : Stamping - General stamping
- Material : Aluminum
Heavy-Walled Flange Milling-Turning Machining and Flaw Detection
- Process : Machining - Turning Milling compound
- Material : Alloy steel
Innovative skiving technology: Breaking through the bottleneck of high-density heat dissipation technology
- Process : Surface treatment - Others
- Material : Alloy steel