Analysis of Centrifugal Fan Blade Machining Process: Key Points of Precision Control and Surface Treatment Technology
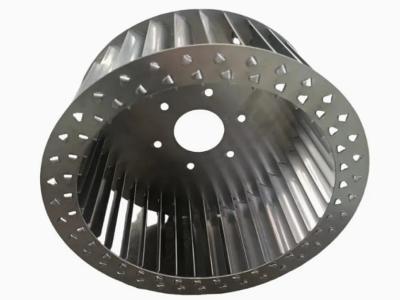
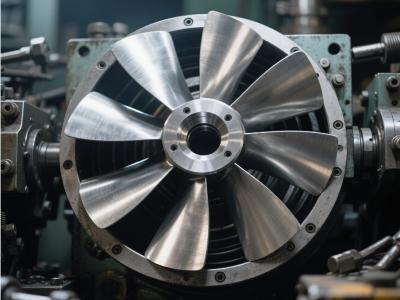
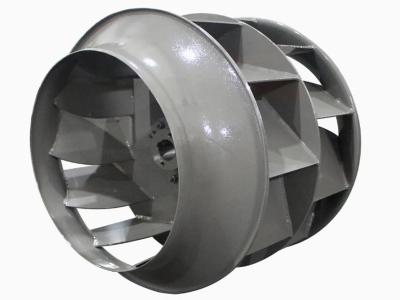
Product name: | Analysis of Centrifugal Fan Blade Machining Process: Key Points of Precision Control and Surface Treatment Technology |
Keywords: | Centrifugal Fan Blade, Machining Process, Precision Control, Surface Treatment, 5-Axis CNC Machining Technology |
Industry: | Mechanical and electrical - Industrial fans and separators, etc. |
Process: | Machining - |
Material: | Alloy steel |
Processing manufacturer
- There are 31 manufacturers that provide similar products
- There are 172 manufacturers that provide this processing technology
- There are 89 manufacturers that provide this material processing service
- There are 148 manufacturers that provide this industry processing service
Product details
The performance of centrifugal fan blades directly affects the efficiency and stability of the fan, and the quality of the machining process directly determines the quality of the blades. In the production process of centrifugal fan blades, precision control and surface treatment are two core technical points.
I. Precision Control Process
The blade shape is complex, and its profile accuracy is related to aerodynamic performance. 5-axis CNC machining technology is the key to ensuring accuracy. Through multi-axis coordinated movement, complex curved surfaces can be precisely cut, and the error can be controlled within ±0.05mm. At the same time, CAD/CAM software needs to be used for simulation before processing to predict the tool path in advance and reduce actual processing errors. In addition, the reasonable design of tooling fixtures is also crucial. Devices such as positioning pins and pressure plates are used to ensure that the centrifugal fan blades are stable during processing and avoid dimensional deviations caused by vibration.
II. Key Points of Surface Treatment Technology
Good surface treatment can improve the wear resistance and corrosion resistance of the blades. The commonly used sandblasting treatment removes the oxide scale on the surface of the centrifugal fan blades and forms a rough texture through high-speed sand particle impact, which enhances the adhesion of the coating. Anodizing technology is suitable for aluminum alloy blades, forming a dense oxide film on the surface, which effectively improves corrosion resistance. For high-performance requirements, thermal spraying technology can also be used to melt and spray wear-resistant alloy powder on the surface of the blades to form a protective layer with a hardness of HV800 or more, which significantly extends the service life of centrifugal fan blades.
III. Quality Inspection and Optimization
After processing is completed, the blades need to be fully dimensionally inspected with equipment such as a three-coordinate measuring machine and a laser scanner, focusing on monitoring key parameters such as blade profile and thickness. If deviations are found, processing parameters can be corrected through error compensation algorithms, or local areas can be reprocessed to ensure that the product meets design requirements.
In the machining of centrifugal fan blades, precision control and surface treatment complement each other. Only by grasping the technical points of both can efficient and durable blades be produced, providing a solid guarantee for the stable operation of the fan.
I. Precision Control Process
The blade shape is complex, and its profile accuracy is related to aerodynamic performance. 5-axis CNC machining technology is the key to ensuring accuracy. Through multi-axis coordinated movement, complex curved surfaces can be precisely cut, and the error can be controlled within ±0.05mm. At the same time, CAD/CAM software needs to be used for simulation before processing to predict the tool path in advance and reduce actual processing errors. In addition, the reasonable design of tooling fixtures is also crucial. Devices such as positioning pins and pressure plates are used to ensure that the centrifugal fan blades are stable during processing and avoid dimensional deviations caused by vibration.
II. Key Points of Surface Treatment Technology
Good surface treatment can improve the wear resistance and corrosion resistance of the blades. The commonly used sandblasting treatment removes the oxide scale on the surface of the centrifugal fan blades and forms a rough texture through high-speed sand particle impact, which enhances the adhesion of the coating. Anodizing technology is suitable for aluminum alloy blades, forming a dense oxide film on the surface, which effectively improves corrosion resistance. For high-performance requirements, thermal spraying technology can also be used to melt and spray wear-resistant alloy powder on the surface of the blades to form a protective layer with a hardness of HV800 or more, which significantly extends the service life of centrifugal fan blades.
III. Quality Inspection and Optimization
After processing is completed, the blades need to be fully dimensionally inspected with equipment such as a three-coordinate measuring machine and a laser scanner, focusing on monitoring key parameters such as blade profile and thickness. If deviations are found, processing parameters can be corrected through error compensation algorithms, or local areas can be reprocessed to ensure that the product meets design requirements.
In the machining of centrifugal fan blades, precision control and surface treatment complement each other. Only by grasping the technical points of both can efficient and durable blades be produced, providing a solid guarantee for the stable operation of the fan.
Previous article : Forged Custom Flanges
Similar products
MoreMachining Process Analysis of Carbon Steel Fixed Anchor Plates
- Process : Machining - CNC milling or milling machining
- Material : Carbon steel
Cone Crusher Mantle
- Process : -
- Material :
What are the machining processes used for processing axial fan housings
- Process : Sheet metal - Welding
- Material : Carbon steel
Precision Machining of U-Steel Profiles for Building Applications
- Process : Stamping - General stamping
- Material : Aluminum
Custom Fabrication of S355JR Welded H-Beams for Construction Projects
- Process : Sheet metal - Welding
- Material : Carbon steel
Heavy-Walled Flange Milling-Turning Machining and Flaw Detection
- Process : Machining - Turning Milling compound
- Material : Alloy steel
Drill Stabilizers Applied in Oil Drilling Platforms
- Process : Machining - Five-axis machining
- Material : Alloy steel
Innovative skiving technology: Breaking through the bottleneck of high-density heat dissipation technology
- Process : Surface treatment - Others
- Material : Alloy steel
More products
MoreMachining Process Analysis of Carbon Steel Fixed Anchor Plates
- Process : Machining - CNC milling or milling machining
- Material : Carbon steel
Cone Crusher Mantle
- Process : -
- Material :
What are the machining processes used for processing axial fan housings
- Process : Sheet metal - Welding
- Material : Carbon steel
Precision Machining of U-Steel Profiles for Building Applications
- Process : Stamping - General stamping
- Material : Aluminum
Custom Fabrication of S355JR Welded H-Beams for Construction Projects
- Process : Sheet metal - Welding
- Material : Carbon steel
Heavy-Walled Flange Milling-Turning Machining and Flaw Detection
- Process : Machining - Turning Milling compound
- Material : Alloy steel
Drill Stabilizers Applied in Oil Drilling Platforms
- Process : Machining - Five-axis machining
- Material : Alloy steel
Innovative skiving technology: Breaking through the bottleneck of high-density heat dissipation technology
- Process : Surface treatment - Others
- Material : Alloy steel