What Machining Processes Are Used to Manufacture Heat Exchanger Tubes
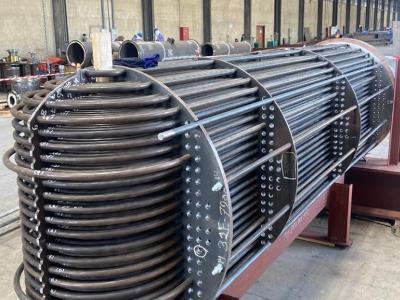
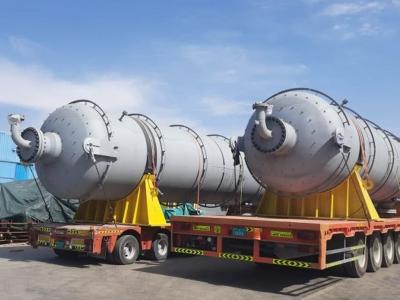
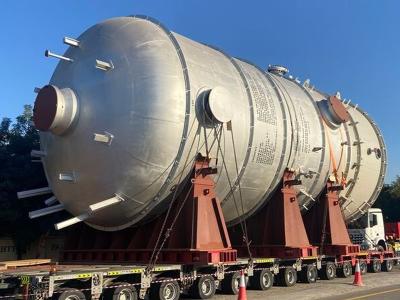
Product name: | What Machining Processes Are Used to Manufacture Heat Exchanger Tubes |
Keywords: | Heat Exchanger Tubes, Heat Exchangers, Heat Exchanger Machining Processes, Thermal Design |
Industry: | Mechanical and electrical - Pressure vessel industry |
Process: | Machining - Turning |
Material: | Alloy steel |
Processing manufacturer
- There are 60 manufacturers that provide similar products
- There are 185 manufacturers that provide this processing technology
- There are 106 manufacturers that provide this material processing service
- There are 200 manufacturers that provide this industry processing service
Product details
The production of heat exchanger tubes involves various machining processes to ensure the tubes precision, surface quality, and performance.
Initially, CNC cutting or laser cutting is preferred to cut the tubes to the designed length, ensuring flat end faces. The tube bending process uses hydraulic or CNC tube bending machines to process the tubes into U-shapes or serpentine shapes, requiring uniform wall thickness control to prevent cracking.
Turning is used to machine the outer diameter or inner bore of the tube ends to ensure connection accuracy.
Drilling is used to machine hole positions on the tube sheet, and in conjunction with the tube expansion process, hydraulic tube expanders are used to tightly connect the tubes to the tube sheet, ensuring sealing performance.
Welding uses argon arc welding or laser welding to connect the tube ends to the tube sheet, and the weld seams require non-destructive testing to ensure quality.
Grinding or polishing improves the surface finish of the inner and outer surfaces of the tubes, reducing fluid resistance and scaling.
Surface treatments such as shot blasting or chemical cleaning remove oxide scale, and some tubes can be sprayed with corrosion-resistant coatings.
Heat treatment uses annealing to eliminate stress and improve material toughness.
CNC machining is used for complex tube ends or hole systems, improving efficiency and accuracy.
These processes need to be selected based on the tube material (such as stainless steel, copper alloy) and the type of heat exchanger, and combined with strict quality control and non-destructive testing to ensure the heat transfer efficiency, corrosion resistance, and service life of the heat exchanger tubes.
Initially, CNC cutting or laser cutting is preferred to cut the tubes to the designed length, ensuring flat end faces. The tube bending process uses hydraulic or CNC tube bending machines to process the tubes into U-shapes or serpentine shapes, requiring uniform wall thickness control to prevent cracking.
Turning is used to machine the outer diameter or inner bore of the tube ends to ensure connection accuracy.
Drilling is used to machine hole positions on the tube sheet, and in conjunction with the tube expansion process, hydraulic tube expanders are used to tightly connect the tubes to the tube sheet, ensuring sealing performance.
Welding uses argon arc welding or laser welding to connect the tube ends to the tube sheet, and the weld seams require non-destructive testing to ensure quality.
Grinding or polishing improves the surface finish of the inner and outer surfaces of the tubes, reducing fluid resistance and scaling.
Surface treatments such as shot blasting or chemical cleaning remove oxide scale, and some tubes can be sprayed with corrosion-resistant coatings.
Heat treatment uses annealing to eliminate stress and improve material toughness.
CNC machining is used for complex tube ends or hole systems, improving efficiency and accuracy.
These processes need to be selected based on the tube material (such as stainless steel, copper alloy) and the type of heat exchanger, and combined with strict quality control and non-destructive testing to ensure the heat transfer efficiency, corrosion resistance, and service life of the heat exchanger tubes.
Previous article : Galvanized Steel Grating for Municipal Drainage Systems: Corrosion-Resistant, Pressure-Resistant, and Safer
Next article : Shafts: Rotating Support Elements
Similar products
MoreMachining Process Analysis of Carbon Steel Fixed Anchor Plates
- Process : Machining - CNC milling or milling machining
- Material : Carbon steel
Precision Machining of U-Steel Profiles for Building Applications
- Process : Stamping - General stamping
- Material : Aluminum
Cone Crusher Mantle
- Process : -
- Material :
What are the machining processes used for processing axial fan housings
- Process : Sheet metal - Welding
- Material : Carbon steel
Heavy-Walled Flange Milling-Turning Machining and Flaw Detection
- Process : Machining - Turning Milling compound
- Material : Alloy steel
Custom Fabrication of S355JR Welded H-Beams for Construction Projects
- Process : Sheet metal - Welding
- Material : Carbon steel
Innovative skiving technology: Breaking through the bottleneck of high-density heat dissipation technology
- Process : Surface treatment - Others
- Material : Alloy steel
Drill Stabilizers Applied in Oil Drilling Platforms
- Process : Machining - Five-axis machining
- Material : Alloy steel
More products
MoreMachining Process Analysis of Carbon Steel Fixed Anchor Plates
- Process : Machining - CNC milling or milling machining
- Material : Carbon steel
Precision Machining of U-Steel Profiles for Building Applications
- Process : Stamping - General stamping
- Material : Aluminum
Cone Crusher Mantle
- Process : -
- Material :
What are the machining processes used for processing axial fan housings
- Process : Sheet metal - Welding
- Material : Carbon steel
Heavy-Walled Flange Milling-Turning Machining and Flaw Detection
- Process : Machining - Turning Milling compound
- Material : Alloy steel
Custom Fabrication of S355JR Welded H-Beams for Construction Projects
- Process : Sheet metal - Welding
- Material : Carbon steel
Innovative skiving technology: Breaking through the bottleneck of high-density heat dissipation technology
- Process : Surface treatment - Others
- Material : Alloy steel
Drill Stabilizers Applied in Oil Drilling Platforms
- Process : Machining - Five-axis machining
- Material : Alloy steel