What Machining Processes Are Used in the Production of Internal Combustion Engine Cylinder Blocks
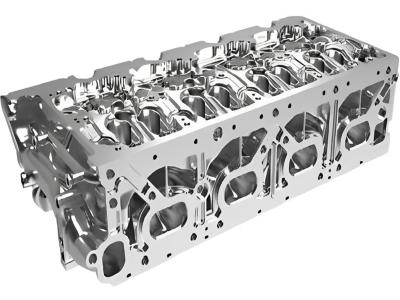
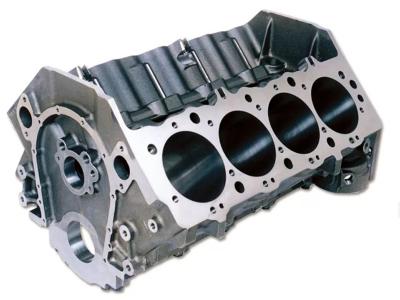
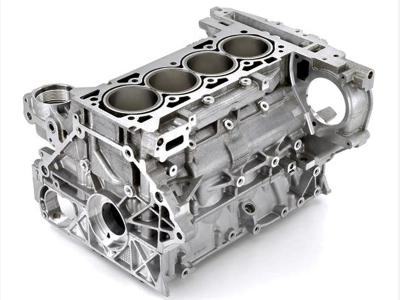
Product name: | What Machining Processes Are Used in the Production of Internal Combustion Engine Cylinder Blocks |
Keywords: | Milling process for machining the plane of the cylinder block, boring process for machining the cylinder bores of the cylinder block, honing process, cylinder block structure |
Industry: | Mechanical and electrical - Pneumatic industry |
Process: | Machining - CNC milling or milling machining |
Material: | Hard alloys |
Processing manufacturer
- There are 52 manufacturers that provide similar products
- There are 154 manufacturers that provide this processing technology
- There are 100 manufacturers that provide this material processing service
- There are 195 manufacturers that provide this industry processing service
Product details
The production of internal combustion engine cylinder blocks involves a variety of machining processes to ensure that their high precision, complex structure, and surface quality meet engine performance requirements.
1. Milling
- Purpose: Machining the planes of the cylinder block, such as the cylinder head mating surface, the crankcase mating surface, and the sides, to ensure flatness and surface finish.
- Equipment: CNC gantry milling machines, vertical/horizontal machining centers.
- Features:
- Rough milling: Removing casting allowance, leaving 2-4mm machining allowance.
- Finish milling: Controlling flatness error within 0.02mm, surface roughness Ra1.6-3.2.
- Application: Machining datum planes and mounting surfaces to provide positioning datums for subsequent processes.
2. Boring
- Purpose: Machining critical hole systems such as cylinder bores, main bearing bores, and camshaft bores of the cylinder block to ensure roundness, cylindricity, and concentricity.
- Equipment: CNC boring machines, precision horizontal boring machines, machining centers.
- Features:
- Rough boring: Rapidly removing material, leaving 0.5-1mm allowance.
- Semi-finish boring: Improving the geometric accuracy of the hole, reducing the allowance to 0.1-0.2mm.
- Finish boring: Achieving design dimensions, controlling roundness error within 0.005-0.01mm.
- Application: High-precision machining of cylinder bores and main bearing bores, affecting the stability of piston movement and crankshaft rotation.
3. Honing
- Purpose: Finishing the inner wall of the cylinder bore to form a cross-hatch pattern (angle 45°-60°) to improve lubricity and wear resistance.
- Equipment: CNC honing machines.
- Features:
- Controlling surface roughness Ra0.2-0.4 to ensure oil film retention.
- Improving the cylindricity and straightness of the cylinder bore, with an error of less than 0.01mm.
- Application: Final finishing of the cylinder bore, directly affecting engine sealing and piston life.
4. Drilling
- Purpose: Machining auxiliary hole systems such as bolt holes, oil passage holes, and water passage holes of the cylinder block.
- Equipment: CNC drilling machines, machining centers.
- Features:
- Rough drilling: Rapidly forming hole positions, leaving allowance.
- Precision drilling or reaming: Ensuring hole position tolerance and surface quality.
- Application: Machining mounting holes and fluid passages, requiring guaranteed positional accuracy.
5. Reaming
- Purpose: Finishing small-diameter holes (such as push rod holes, locating pin holes) to improve hole size accuracy and surface finish.
- Equipment: CNC machining centers, dedicated reaming machines.
- Features: Tolerance controlled within IT6-IT7, surface roughness Ra0.8-1.6.
- Application: Machining high-precision mating holes, such as finishing camshaft bores.
6. Grinding
- Purpose: Finishing planes or hole systems, such as the cylinder head mating surface or the inner surface of the main bearing bore, to ensure extremely high flatness or roundness.
- Equipment: Surface grinders, guideway grinders, internal cylindrical grinders.
- Features: Flatness error less than 0.01mm, surface roughness Ra0.4-0.8.
- Application: Used for surfaces requiring extremely high precision, such as the cylinder head mating surface or the inner surface of cast iron cylinder liners.
7. Tapping
- Purpose: Machining threaded holes on the cylinder block for installing bolts or screws.
- Equipment: CNC machining centers, tapping machines.
- Features: Ensuring thread accuracy (such as M6-M12 threads), avoiding burrs affecting assembly.
- Application: Machining cylinder head bolt holes, accessory mounting holes, etc.
8. Broaching (Less Commonly Used)
- Purpose: Machining complex internal holes or keyways (such as certain special oil passages or locating grooves).
- Equipment: Broaching machines.
- Features: Efficiently machining complex shapes, high precision but high cost.
- Application: Used for cylinder blocks with specific structures, such as special groove machining for high-performance engines.
Previous article : Welded Box Columns: Supporting High-Strength Engineering for Stable Upward Progress
Next article : Centralizer Anti-Wear Design
Similar products
MoreMachining Process Analysis of Carbon Steel Fixed Anchor Plates
- Process : Machining - CNC milling or milling machining
- Material : Carbon steel
Cone Crusher Mantle
- Process : -
- Material :
Custom Fabrication of S355JR Welded H-Beams for Construction Projects
- Process : Sheet metal - Welding
- Material : Carbon steel
What are the machining processes used for processing axial fan housings
- Process : Sheet metal - Welding
- Material : Carbon steel
Drill Stabilizers Applied in Oil Drilling Platforms
- Process : Machining - Five-axis machining
- Material : Alloy steel
Precision Machining of U-Steel Profiles for Building Applications
- Process : Stamping - General stamping
- Material : Aluminum
Heavy-Walled Flange Milling-Turning Machining and Flaw Detection
- Process : Machining - Turning Milling compound
- Material : Alloy steel
Innovative skiving technology: Breaking through the bottleneck of high-density heat dissipation technology
- Process : Surface treatment - Others
- Material : Alloy steel
More products
MoreMachining Process Analysis of Carbon Steel Fixed Anchor Plates
- Process : Machining - CNC milling or milling machining
- Material : Carbon steel
Cone Crusher Mantle
- Process : -
- Material :
Custom Fabrication of S355JR Welded H-Beams for Construction Projects
- Process : Sheet metal - Welding
- Material : Carbon steel
What are the machining processes used for processing axial fan housings
- Process : Sheet metal - Welding
- Material : Carbon steel
Drill Stabilizers Applied in Oil Drilling Platforms
- Process : Machining - Five-axis machining
- Material : Alloy steel
Precision Machining of U-Steel Profiles for Building Applications
- Process : Stamping - General stamping
- Material : Aluminum
Heavy-Walled Flange Milling-Turning Machining and Flaw Detection
- Process : Machining - Turning Milling compound
- Material : Alloy steel
Innovative skiving technology: Breaking through the bottleneck of high-density heat dissipation technology
- Process : Surface treatment - Others
- Material : Alloy steel