What are the types of centralizers?
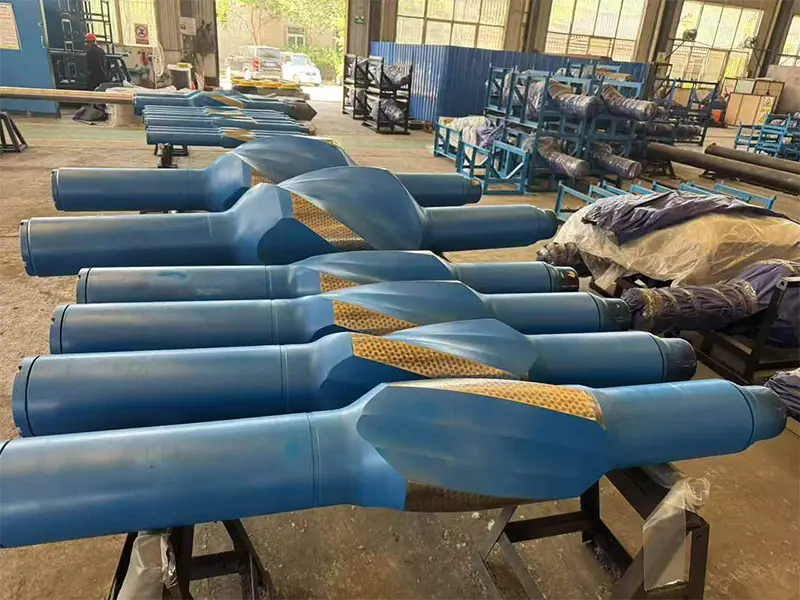
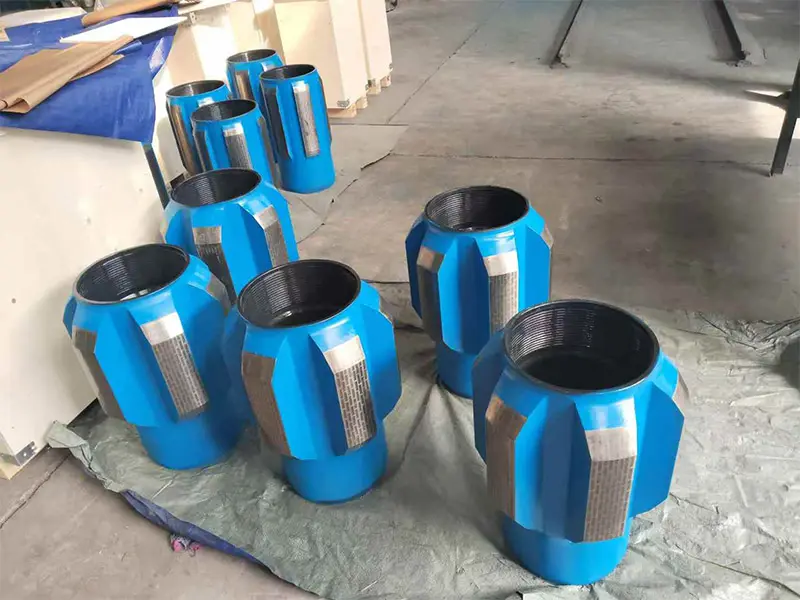
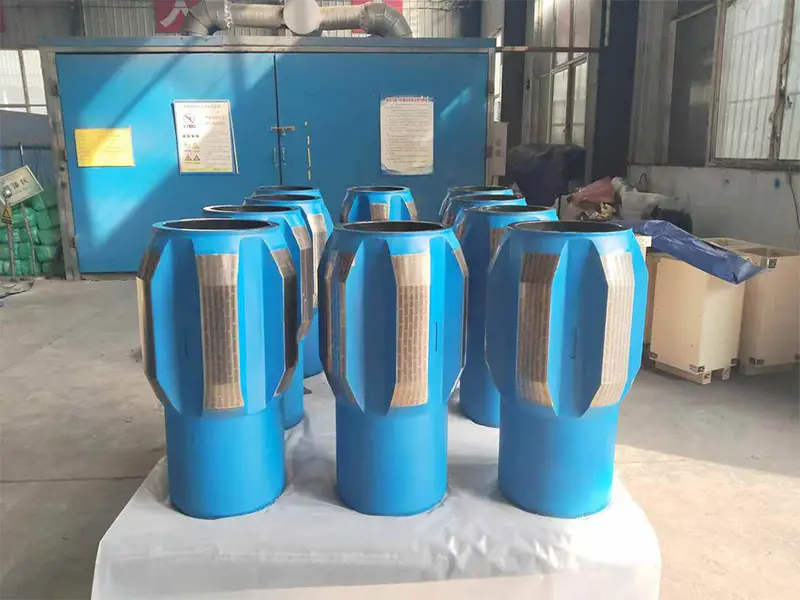
Product name: | What are the types of centralizers? |
Keywords: | What are the types of centralizers? |
Industry: | Petroleum, natural gas and chemical industry - Petroleum and natural gas industry |
Process: | Machining - Five-axis machining |
Material: | Carbon steel |
Processing manufacturer
- There are 44 manufacturers that provide similar products
- There are 131 manufacturers that provide this processing technology
- There are 76 manufacturers that provide this material processing service
- There are 166 manufacturers that provide this industry processing service
Product details
Centralizers are mainly used in oil drilling, completion, and other projects to ensure the central position of casing or drill pipe in the wellbore. According to structure and use, the types of centralizers mainly include the following:
- Bow Spring Centralizer
- Features: Consists of bow spring blades, has strong elasticity, and can adapt to changes in wellbore size.
- Uses: Commonly used in irregular wellbores or deviated wells, and is common in vertical and horizontal wells.
- Advantages: Simple to install, highly adaptable; Disadvantages: Support force may be insufficient to cope with complex well conditions.
- Rigid Centralizer
- Features: Made of rigid materials (such as steel or aluminum), with a fixed structure and high strength.
- Uses: Suitable for regular wellbores or well sections that require high-strength support, such as deep wells or high-temperature and high-pressure wells.
- Advantages: Good stability, wear resistance; Disadvantages: High requirements for wellbore size, poor adaptability.
- Semi-Rigid Centralizer
- Features: Combines the characteristics of bow spring and rigid centralizers, with both elasticity and rigidity.
- Uses: Suitable for complex wellbore conditions, such as medium-deep wells or slightly irregular wellbores.
- Advantages: Balances flexibility and strength; Disadvantages: Higher cost.
- Composite Centralizer
- Features: Made of lightweight composite materials (such as polymer), corrosion-resistant, and lightweight.
- Uses: Commonly used in offshore drilling or corrosive environments.
- Advantages: Reduces casing wear, easy to transport; Disadvantages: Strength may be lower than metal centralizers.
- Integral Centralizer
- Features: Directly integrated with the casing or drill string, no additional installation required.
- Uses: Suitable for efficient operations that require fewer installation steps.
- Advantages: Easy to install, reduces the risk of loosening; Disadvantages: Higher manufacturing cost.
- Non-Welded or Slip-On Centralizer
- Features: Installed on the casing by sliding or snapping, non-welded fixed.
- Uses: Suitable for scenarios that require flexible adjustment of position.
- Advantages: Flexible installation; Disadvantages: There may be a risk of sliding.
- Welded Centralizer
- Features: Fixed on the casing by welding, with a firm connection.
- Uses: Suitable for well sections with high strength requirements, such as deep wells or high-pressure wells.
- Advantages: Strong stability; Disadvantages: Complex installation, difficult to adjust.
- Rotating Centralizer
- Features: Allows the casing to rotate within the centralizer, reducing friction.
- Uses: Commonly used in horizontal wells or long-distance well sections to improve cement sheath quality.
- Advantages: Reduces torque and drag; Disadvantages: Complex structure, higher cost.
The above classification is based on the structure, material, and function of the centralizer. Different types can be selected and used according to well conditions and operation requirements.
Previous article : 42CrMo4, 42CrMo Marine Forgings, Marine Crankshafts, Marine Connecting Rods
Next article : High-Strength Alloy Steel Forged Marine Crankshaft
Similar products
MoreMachining Process Analysis of Carbon Steel Fixed Anchor Plates
- Process : Machining - CNC milling or milling machining
- Material : Carbon steel
Innovative skiving technology: Breaking through the bottleneck of high-density heat dissipation technology
- Process : Surface treatment - Others
- Material : Alloy steel
What are the machining processes used for processing axial fan housings
- Process : Sheet metal - Welding
- Material : Carbon steel
Custom Fabrication of S355JR Welded H-Beams for Construction Projects
- Process : Sheet metal - Welding
- Material : Carbon steel
Heavy-Walled Flange Milling-Turning Machining and Flaw Detection
- Process : Machining - Turning Milling compound
- Material : Alloy steel
Cone Crusher Mantle
- Process : -
- Material :
Precision Machining of U-Steel Profiles for Building Applications
- Process : Stamping - General stamping
- Material : Aluminum
Drill Stabilizers Applied in Oil Drilling Platforms
- Process : Machining - Five-axis machining
- Material : Alloy steel
More products
MoreMachining Process Analysis of Carbon Steel Fixed Anchor Plates
- Process : Machining - CNC milling or milling machining
- Material : Carbon steel
Innovative skiving technology: Breaking through the bottleneck of high-density heat dissipation technology
- Process : Surface treatment - Others
- Material : Alloy steel
What are the machining processes used for processing axial fan housings
- Process : Sheet metal - Welding
- Material : Carbon steel
Custom Fabrication of S355JR Welded H-Beams for Construction Projects
- Process : Sheet metal - Welding
- Material : Carbon steel
Heavy-Walled Flange Milling-Turning Machining and Flaw Detection
- Process : Machining - Turning Milling compound
- Material : Alloy steel
Cone Crusher Mantle
- Process : -
- Material :
Precision Machining of U-Steel Profiles for Building Applications
- Process : Stamping - General stamping
- Material : Aluminum
Drill Stabilizers Applied in Oil Drilling Platforms
- Process : Machining - Five-axis machining
- Material : Alloy steel