Pneumatic Tire Clutch for Oil Drilling
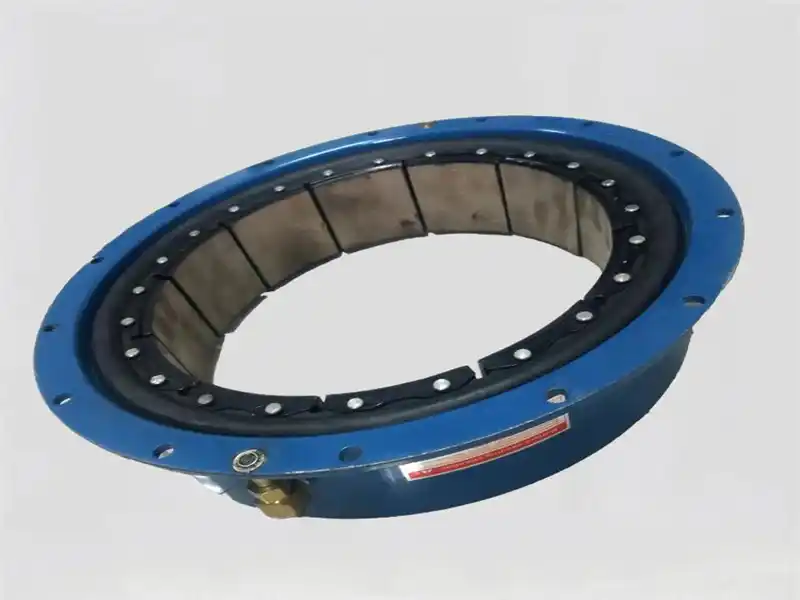
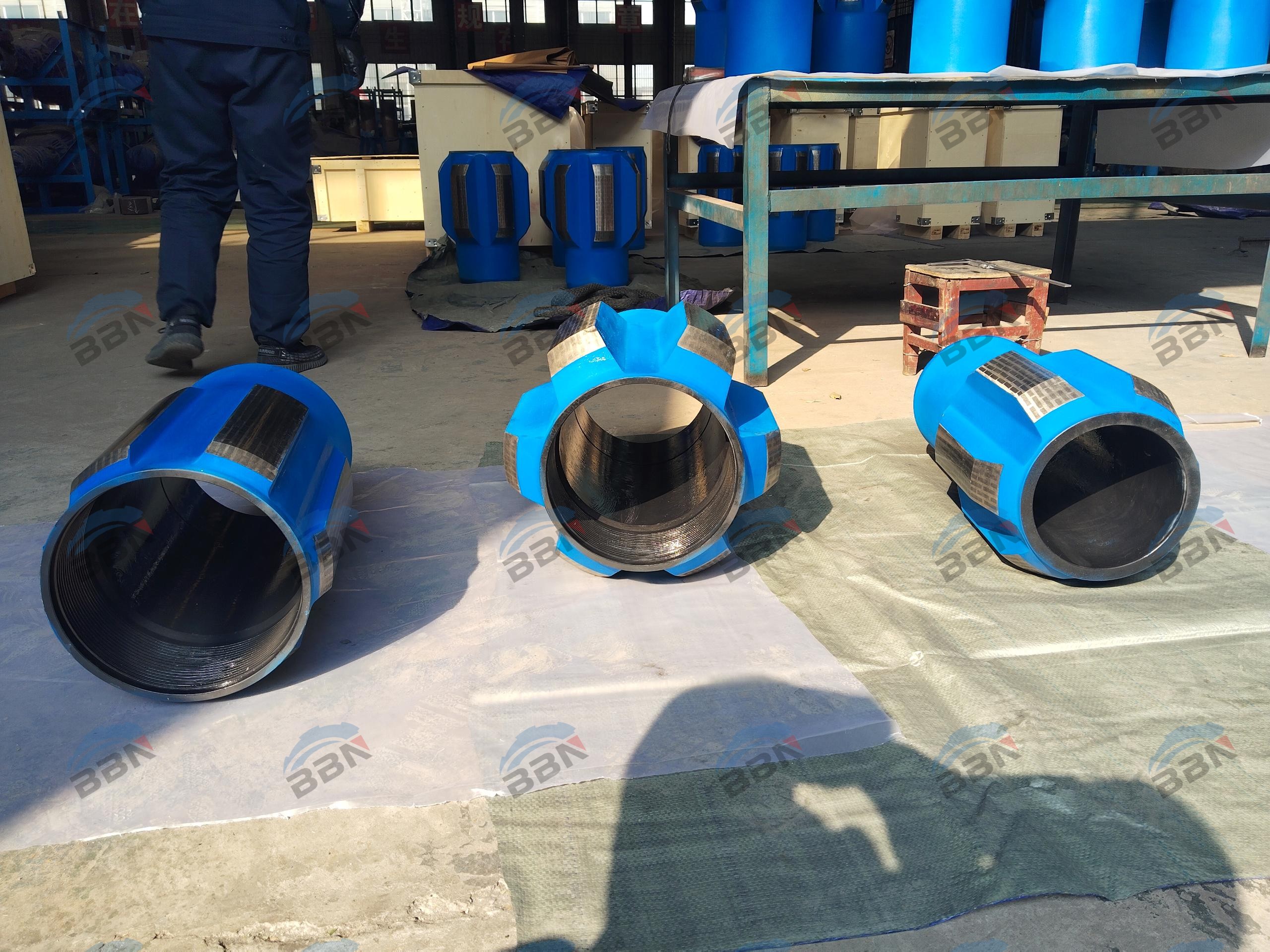
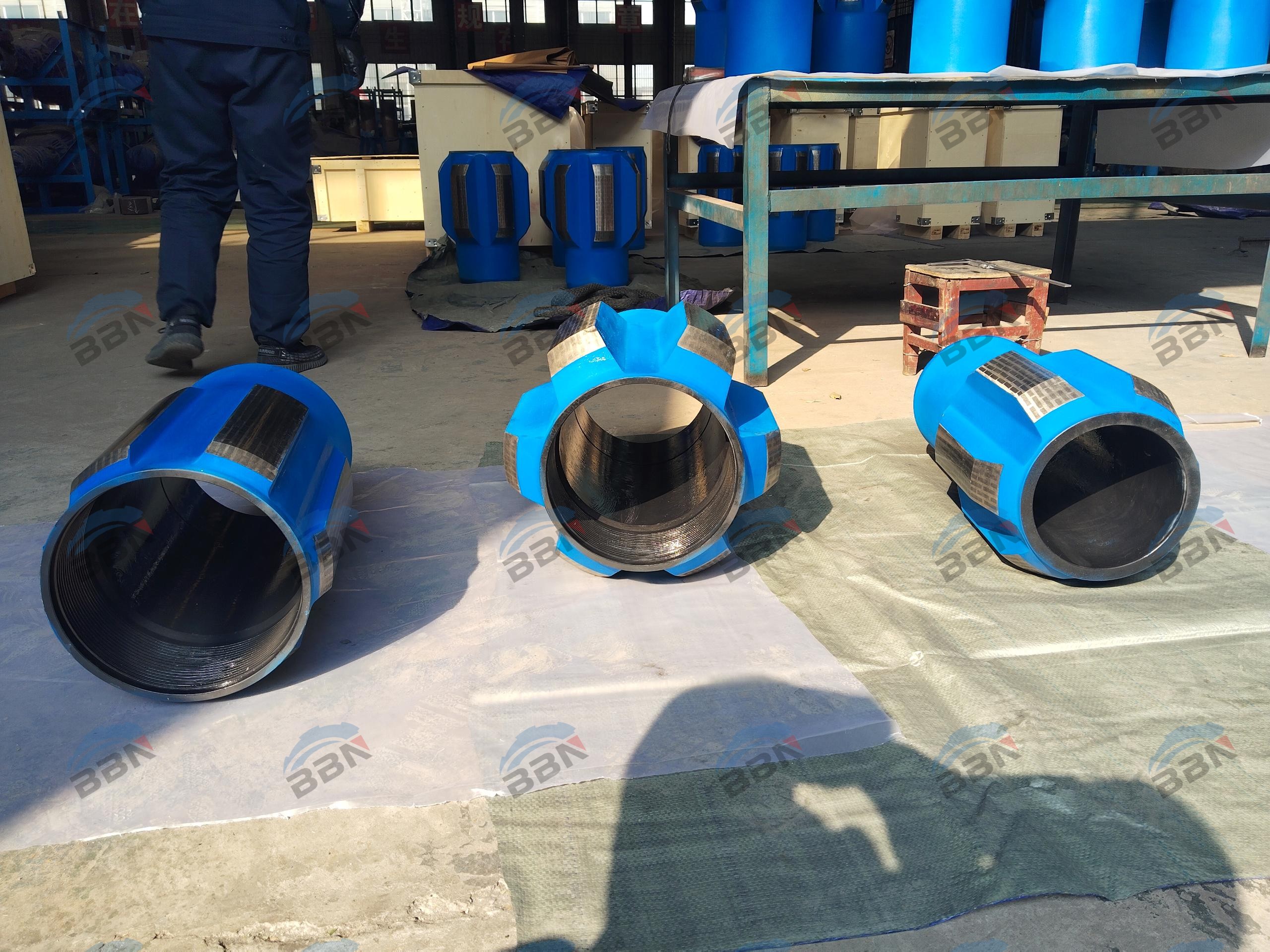
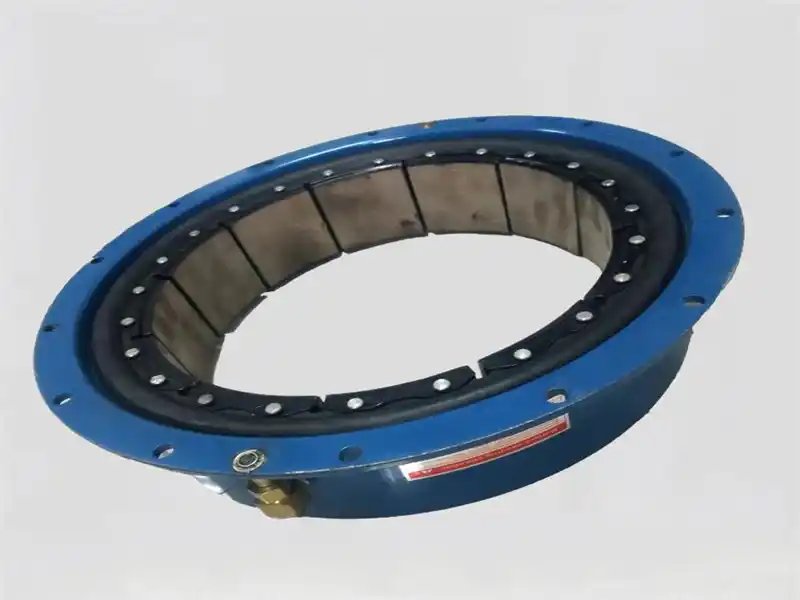
Product name: | Pneumatic Tire Clutch for Oil Drilling |
Keywords: | Pneumatic Tire Clutch |
Industry: | Construction and building materials - Construction industry |
Process: | Machining - Five-axis machining |
Material: | Alloy steel |
Processing manufacturer
- There are 46 manufacturers that provide similar products
- There are 152 manufacturers that provide this processing technology
- There are 89 manufacturers that provide this material processing service
- There are 154 manufacturers that provide this industry processing service
Product details
Pneumatic tire clutches are specifically designed for oil drilling applications and are essential components in drilling rigs for transmitting power and controlling the rotation of the drill string. This clutch mechanism ensures efficient and reliable operation in various drilling operations.
Key Features
Power Transmission and Control: Pneumatic tire clutches facilitate the transmission of power from the prime mover to the drill string, enabling the rotation required for drilling. It provides precise control over power engagement and disengagement, allowing for efficient operation and quick response to changing drilling conditions.
High Load Capacity: The clutch is designed to handle the heavy loads and high torque requirements encountered in oil drilling operations. It offers excellent load-bearing capacity, ensuring reliable performance even under demanding drilling conditions.
Customizable Specifications: Pneumatic tire clutches are available in various specifications to suit different drilling rig models and operational needs. Common parameters include bore diameter, outer diameter, number of tires, tire width, and operating pressure. Customization allows for compatibility with specific rig configurations and desired torque capacity.
Robust Construction and Reliable Performance: These clutches are manufactured using high-quality materials and precision machining techniques to ensure durability and reliable performance in harsh drilling environments. They can withstand extreme temperatures, resist wear and tear, and provide consistent power transmission over extended periods.
Specifications
Standard dimensions for pneumatic tire clutches may vary based on industry standards and manufacturer guidelines. Typical bore diameters range from a few centimeters to several decimeters, while outer diameters vary depending on the torque capacity and drilling rig requirements. The number of tires is selected based on the desired load-bearing capacity. Standard sizes are determined based on compatibility with drilling rig models and industry practices.
Materials and Manufacturing Processes
Pneumatic tire clutches are primarily constructed from high-strength steel or composite materials to withstand heavy loads and provide excellent wear resistance. The tire portion typically consists of a durable rubber compound with high friction characteristics and temperature resistance. Manufacturing processes involve precision machining techniques such as turning, grinding, and bonding to achieve accurate dimensions and secure tire attachment. Surface treatments may be applied to enhance corrosion resistance and overall performance.
Technical Structure Features
The pneumatic tire clutch consists of a central hub with a bore for shaft connection and multiple tires arranged around the circumference. When engaged, the tires make contact with the corresponding surface, transmitting power and controlling the rotation of the drill string. The clutch design ensures reliable engagement, efficient power transfer, and minimal slippage under load.
Installation and Usage
Pneumatic tire clutches are installed within the power transmission system of drilling rigs, typically integrated into the rotary assembly. It is precisely aligned and securely mounted using appropriate fastening methods to ensure proper engagement and reliable power transmission. During operation, the clutch controls the rotation of the drill string by engaging or disengaging power as needed. Regular maintenance, including lubrication and inspection, ensures optimal clutch performance and prolongs the lifespan of clutch components.
Similar products
MoreMachining Process Analysis of Carbon Steel Fixed Anchor Plates
- Process : Machining - CNC milling or milling machining
- Material : Carbon steel
Custom Fabrication of S355JR Welded H-Beams for Construction Projects
- Process : Sheet metal - Welding
- Material : Carbon steel
Cone Crusher Mantle
- Process : -
- Material :
What are the machining processes used for processing axial fan housings
- Process : Sheet metal - Welding
- Material : Carbon steel
Precision Machining of U-Steel Profiles for Building Applications
- Process : Stamping - General stamping
- Material : Aluminum
Drill Stabilizers Applied in Oil Drilling Platforms
- Process : Machining - Five-axis machining
- Material : Alloy steel
Heavy-Walled Flange Milling-Turning Machining and Flaw Detection
- Process : Machining - Turning Milling compound
- Material : Alloy steel
Innovative skiving technology: Breaking through the bottleneck of high-density heat dissipation technology
- Process : Surface treatment - Others
- Material : Alloy steel
More products
MoreMachining Process Analysis of Carbon Steel Fixed Anchor Plates
- Process : Machining - CNC milling or milling machining
- Material : Carbon steel
Custom Fabrication of S355JR Welded H-Beams for Construction Projects
- Process : Sheet metal - Welding
- Material : Carbon steel
Cone Crusher Mantle
- Process : -
- Material :
What are the machining processes used for processing axial fan housings
- Process : Sheet metal - Welding
- Material : Carbon steel
Precision Machining of U-Steel Profiles for Building Applications
- Process : Stamping - General stamping
- Material : Aluminum
Drill Stabilizers Applied in Oil Drilling Platforms
- Process : Machining - Five-axis machining
- Material : Alloy steel
Heavy-Walled Flange Milling-Turning Machining and Flaw Detection
- Process : Machining - Turning Milling compound
- Material : Alloy steel
Innovative skiving technology: Breaking through the bottleneck of high-density heat dissipation technology
- Process : Surface treatment - Others
- Material : Alloy steel