Manufacturing Process of Automotive Leaf Spring Products
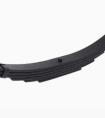
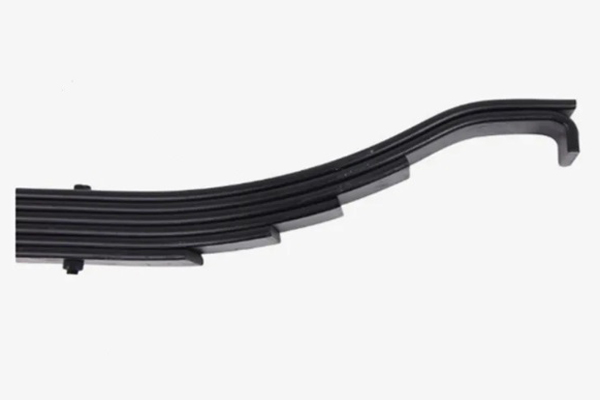
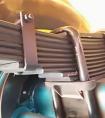
Product name: | Manufacturing Process of Automotive Leaf Spring Products |
Keywords: | Automotive Leaf Spring, Leaf Spring, Leaf Spring, Leaf Spring Plate |
Industry: | Mechanical and electrical - Machine tool, machinery and equipment manufacturing industry |
Process: | Sheet metal - Various types of cutting |
Material: | Bearing steel/spring steel |
Processing manufacturer
- There are 32 manufacturers that provide similar products
- There are 162 manufacturers that provide this processing technology
- There are 61 manufacturers that provide this material processing service
- There are 139 manufacturers that provide this industry processing service
Product details
Automotive leaf springs (also known as leaf springs) are critical load-bearing and vibration-damping components in traditional vehicle suspension systems. Their manufacturing process is complex and demanding, with the core objective of achieving high strength, high fatigue life, and excellent elastic properties.
High-strength hot-rolled spring steel strip coils or fixed-length straight bars are typically selected, such as 60Si2MnA, 50CrVA, 55Cr3, SUP series, etc. The materials must meet strict chemical composition and mechanical property standards.
The inspected spring steel raw material is cut using a circular saw or band saw. Laser cutting or water jet cutting can also be used, but the cost is higher. The cutting step must ensure length accuracy and end face quality (perpendicularity, flatness) and reduce burrs.
The cut steel strip is heated to the austenitizing temperature range to prepare for hot forming. This process requires strict control of heating temperature and time (usually around 900°C - 950°C, depending on the material) to avoid overheating, burning, or decarburization.
The heated steel strip is placed in a roll forging machine and rolled into leaf spring plates with a preset curvature (spring eye) and variable cross-section (main leaf) or constant cross-section (helper leaf) shape. This is a crucial step in obtaining the required stiffness and stress distribution.
The formed leaf spring plate, still in the austenitic state, is quickly transferred to a quenching oil tank for immersion cooling to obtain a high-hardness martensitic structure, laying the foundation for subsequent tempering to achieve high strength and high elasticity.
The quenched leaf spring plate is heated to a specific temperature (usually around 400°C - 500°C, depending on the material and requirements), held for a sufficient time, and then cooled (usually air-cooled). This eliminates quenching stress, improves toughness and plasticity, and obtains the comprehensive mechanical properties required for the leaf spring.
The tempered leaf spring plate is fed into a pass-through or suspension shot peening machine, where the surface is bombarded with a high-speed stream of shot, introducing a beneficial layer of residual compressive stress and improving the surface microstructure. This is one of the most critical processes for improving the fatigue life of the leaf spring.
Drilling or reaming is performed on the spring eye of the main leaf to ensure the dimensional accuracy and surface roughness of the pin hole. Chamfering, grinding, and other processes can be performed on the non-spring eye end to remove burrs and improve assembly.
Using a pre-stressing machine (hydraulic or mechanical), a single leaf spring (or sometimes a multi-leaf combination) is placed in a fixture and subjected to a load exceeding the design full load several times (e.g., 2-3 times) to cause plastic deformation. After unloading, the required positive arch height is obtained, improving the stress distribution and inter-leaf friction during the operation of the automotive leaf spring and increasing fatigue life.
Multiple leaf springs (main leaf, helper leaf) are stacked in order and fixed together with a center bolt or clamp (rebound clip). Grease is applied between the leaves or anti-friction liners/sliders are installed to reduce inter-leaf friction, wear, and noise.
To ensure the durability of the leaf spring under harsh conditions, painting, baking varnish, plastic spraying, or zinc-chromium coating is usually applied to the surface of the leaf spring.
Before delivery, finished product sampling inspections are also required to ensure that the dimensions and quality of the product meet customer requirements.
The manufacturing of automotive leaf springs is a complex process that integrates materials science, plastic processing, heat treatment, surface engineering, and precision testing. Each process is closely linked and jointly determines the strength, elasticity, fatigue life, and durability of the final product. As the automotive industrys requirements for safety, comfort, lightweighting, and long life continue to increase, the processing technology of leaf springs is also continuously developing and optimizing. Strict quality control and continuous innovation are key to ensuring that leaf springs meet the stringent usage requirements of modern automobiles.
High-strength hot-rolled spring steel strip coils or fixed-length straight bars are typically selected, such as 60Si2MnA, 50CrVA, 55Cr3, SUP series, etc. The materials must meet strict chemical composition and mechanical property standards.
The inspected spring steel raw material is cut using a circular saw or band saw. Laser cutting or water jet cutting can also be used, but the cost is higher. The cutting step must ensure length accuracy and end face quality (perpendicularity, flatness) and reduce burrs.
The cut steel strip is heated to the austenitizing temperature range to prepare for hot forming. This process requires strict control of heating temperature and time (usually around 900°C - 950°C, depending on the material) to avoid overheating, burning, or decarburization.
The heated steel strip is placed in a roll forging machine and rolled into leaf spring plates with a preset curvature (spring eye) and variable cross-section (main leaf) or constant cross-section (helper leaf) shape. This is a crucial step in obtaining the required stiffness and stress distribution.
The formed leaf spring plate, still in the austenitic state, is quickly transferred to a quenching oil tank for immersion cooling to obtain a high-hardness martensitic structure, laying the foundation for subsequent tempering to achieve high strength and high elasticity.
The quenched leaf spring plate is heated to a specific temperature (usually around 400°C - 500°C, depending on the material and requirements), held for a sufficient time, and then cooled (usually air-cooled). This eliminates quenching stress, improves toughness and plasticity, and obtains the comprehensive mechanical properties required for the leaf spring.
The tempered leaf spring plate is fed into a pass-through or suspension shot peening machine, where the surface is bombarded with a high-speed stream of shot, introducing a beneficial layer of residual compressive stress and improving the surface microstructure. This is one of the most critical processes for improving the fatigue life of the leaf spring.
Drilling or reaming is performed on the spring eye of the main leaf to ensure the dimensional accuracy and surface roughness of the pin hole. Chamfering, grinding, and other processes can be performed on the non-spring eye end to remove burrs and improve assembly.
Using a pre-stressing machine (hydraulic or mechanical), a single leaf spring (or sometimes a multi-leaf combination) is placed in a fixture and subjected to a load exceeding the design full load several times (e.g., 2-3 times) to cause plastic deformation. After unloading, the required positive arch height is obtained, improving the stress distribution and inter-leaf friction during the operation of the automotive leaf spring and increasing fatigue life.
Multiple leaf springs (main leaf, helper leaf) are stacked in order and fixed together with a center bolt or clamp (rebound clip). Grease is applied between the leaves or anti-friction liners/sliders are installed to reduce inter-leaf friction, wear, and noise.
To ensure the durability of the leaf spring under harsh conditions, painting, baking varnish, plastic spraying, or zinc-chromium coating is usually applied to the surface of the leaf spring.
Before delivery, finished product sampling inspections are also required to ensure that the dimensions and quality of the product meet customer requirements.
The manufacturing of automotive leaf springs is a complex process that integrates materials science, plastic processing, heat treatment, surface engineering, and precision testing. Each process is closely linked and jointly determines the strength, elasticity, fatigue life, and durability of the final product. As the automotive industrys requirements for safety, comfort, lightweighting, and long life continue to increase, the processing technology of leaf springs is also continuously developing and optimizing. Strict quality control and continuous innovation are key to ensuring that leaf springs meet the stringent usage requirements of modern automobiles.
Similar products
MoreMachining Process Analysis of Carbon Steel Fixed Anchor Plates
- Process : Machining - CNC milling or milling machining
- Material : Carbon steel
Cone Crusher Mantle
- Process : -
- Material :
What are the machining processes used for processing axial fan housings
- Process : Sheet metal - Welding
- Material : Carbon steel
Precision Machining of U-Steel Profiles for Building Applications
- Process : Stamping - General stamping
- Material : Aluminum
Custom Fabrication of S355JR Welded H-Beams for Construction Projects
- Process : Sheet metal - Welding
- Material : Carbon steel
Heavy-Walled Flange Milling-Turning Machining and Flaw Detection
- Process : Machining - Turning Milling compound
- Material : Alloy steel
Drill Stabilizers Applied in Oil Drilling Platforms
- Process : Machining - Five-axis machining
- Material : Alloy steel
Innovative skiving technology: Breaking through the bottleneck of high-density heat dissipation technology
- Process : Surface treatment - Others
- Material : Alloy steel
More products
MoreMachining Process Analysis of Carbon Steel Fixed Anchor Plates
- Process : Machining - CNC milling or milling machining
- Material : Carbon steel
Cone Crusher Mantle
- Process : -
- Material :
What are the machining processes used for processing axial fan housings
- Process : Sheet metal - Welding
- Material : Carbon steel
Precision Machining of U-Steel Profiles for Building Applications
- Process : Stamping - General stamping
- Material : Aluminum
Custom Fabrication of S355JR Welded H-Beams for Construction Projects
- Process : Sheet metal - Welding
- Material : Carbon steel
Heavy-Walled Flange Milling-Turning Machining and Flaw Detection
- Process : Machining - Turning Milling compound
- Material : Alloy steel
Drill Stabilizers Applied in Oil Drilling Platforms
- Process : Machining - Five-axis machining
- Material : Alloy steel
Innovative skiving technology: Breaking through the bottleneck of high-density heat dissipation technology
- Process : Surface treatment - Others
- Material : Alloy steel