Machining Processes Involved in Manufacturing Industrial Boiler Water Walls
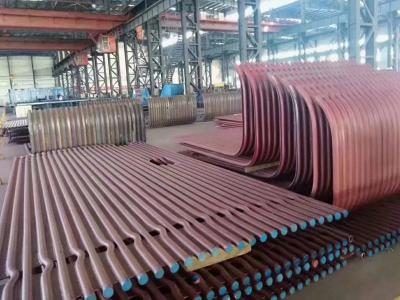
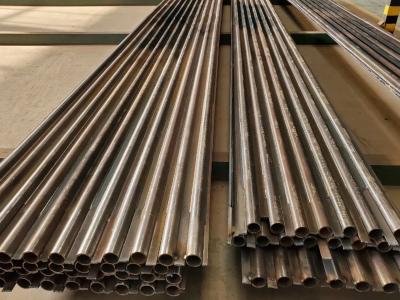
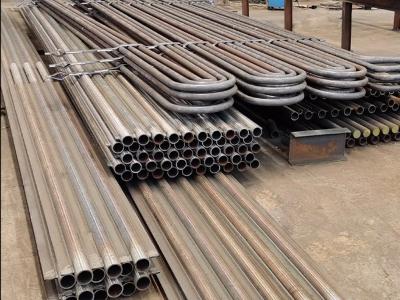
Product name: | Machining Processes Involved in Manufacturing Industrial Boiler Water Walls |
Keywords: | Industrial boiler water wall, boiler water wall, manufacturing industrial boiler water wall, water wall machining process |
Industry: | Mechanical and electrical - Boiler industry |
Process: | Machining - CNC milling or milling machining |
Material: | Alloy steel |
Processing manufacturer
- There are 40 manufacturers that provide similar products
- There are 132 manufacturers that provide this processing technology
- There are 105 manufacturers that provide this material processing service
- There are 106 manufacturers that provide this industry processing service
Product details
The machining processes involved in manufacturing industrial boiler water walls mainly include the following:
- Tube Cutting: Using sawing, plasma cutting, or laser cutting processes to cut seamless steel tubes to the required length, ensuring flat end faces.
- Tube Bending: Using a tube bending machine to cold bend or hot bend the water wall tubes to form the required curved shapes, such as serpentine tubes or membrane wall structures.
- Turning: Used to machine the outer diameter, inner diameter, or chamfer of the water wall tube ends to meet welding or connection requirements, usually performed on a lathe.
- Drilling: Drilling holes in the tubes or headers of the water wall for installing connecting pipes, nozzles, or other connecting parts, commonly used in header manufacturing.
- Milling: Used to machine the plane, groove, or connecting surface of the water wall header to ensure assembly accuracy, often using a milling machine or CNC machining center.
- Post-Welding Machining: Water walls are usually composed of tubes and flat steel bars welded together (such as membrane water walls). The weld seams may need to be milled, ground, or turned to remove excess height, flatten the surface, or eliminate defects.
- Roller Burnishing: Used for surface strengthening of the inner wall of the tubes to improve wear resistance and corrosion resistance, especially in high-pressure boiler water walls.
- Tube Expansion: Connecting water wall tubes to headers or tube sheets through mechanical or hydraulic tube expansion processes to ensure sealing and strength.
- Grinding: Used to finish the connecting surfaces of tube ends or headers to improve surface finish and dimensional accuracy, especially in high-precision assemblies.
- CNC Machining: Modern water wall manufacturing often uses CNC equipment (such as CNC lathes, machining centers) to process complex shapes, such as the hole system or complex curved surfaces of headers.
- Stamping or Extrusion: For the flat steel bars or some pipe fittings of membrane water walls, stamping or extrusion molding may be required to meet specific shape requirements.
The selection of these processes depends on the structural form of the water wall (bare tube, membrane wall, etc.), material (such as carbon steel, low alloy steel), and the boilers working pressure and temperature requirements. Non-destructive testing (such as ultrasonic or radiographic testing) is usually used during the processing to ensure the quality of welds and machining.
Next article : Universal Oil Machinery Well Brake Pads
Similar products
MoreMachining Process Analysis of Carbon Steel Fixed Anchor Plates
- Process : Machining - CNC milling or milling machining
- Material : Carbon steel
What are the machining processes used for processing axial fan housings
- Process : Sheet metal - Welding
- Material : Carbon steel
Heavy-Walled Flange Milling-Turning Machining and Flaw Detection
- Process : Machining - Turning Milling compound
- Material : Alloy steel
Precision Machining of U-Steel Profiles for Building Applications
- Process : Stamping - General stamping
- Material : Aluminum
Cone Crusher Mantle
- Process : -
- Material :
Custom Fabrication of S355JR Welded H-Beams for Construction Projects
- Process : Sheet metal - Welding
- Material : Carbon steel
Innovative skiving technology: Breaking through the bottleneck of high-density heat dissipation technology
- Process : Surface treatment - Others
- Material : Alloy steel
Drill Stabilizers Applied in Oil Drilling Platforms
- Process : Machining - Five-axis machining
- Material : Alloy steel
More products
MoreMachining Process Analysis of Carbon Steel Fixed Anchor Plates
- Process : Machining - CNC milling or milling machining
- Material : Carbon steel
What are the machining processes used for processing axial fan housings
- Process : Sheet metal - Welding
- Material : Carbon steel
Heavy-Walled Flange Milling-Turning Machining and Flaw Detection
- Process : Machining - Turning Milling compound
- Material : Alloy steel
Precision Machining of U-Steel Profiles for Building Applications
- Process : Stamping - General stamping
- Material : Aluminum
Cone Crusher Mantle
- Process : -
- Material :
Custom Fabrication of S355JR Welded H-Beams for Construction Projects
- Process : Sheet metal - Welding
- Material : Carbon steel
Innovative skiving technology: Breaking through the bottleneck of high-density heat dissipation technology
- Process : Surface treatment - Others
- Material : Alloy steel
Drill Stabilizers Applied in Oil Drilling Platforms
- Process : Machining - Five-axis machining
- Material : Alloy steel