High-Temperature Alloy Forging for Engine Turbine Blades
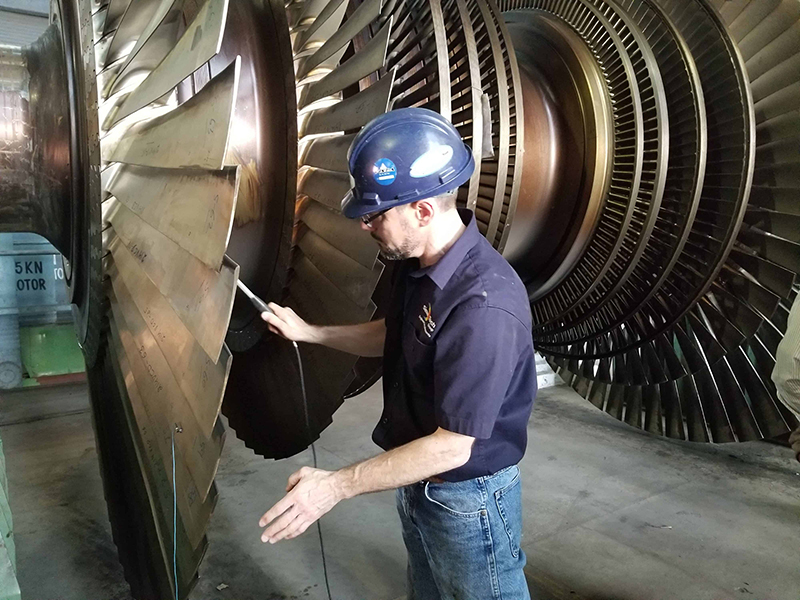
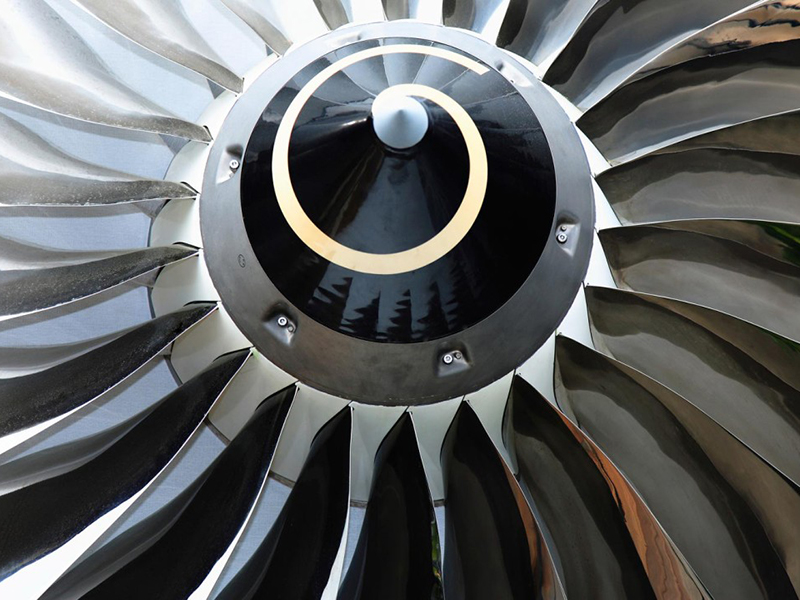
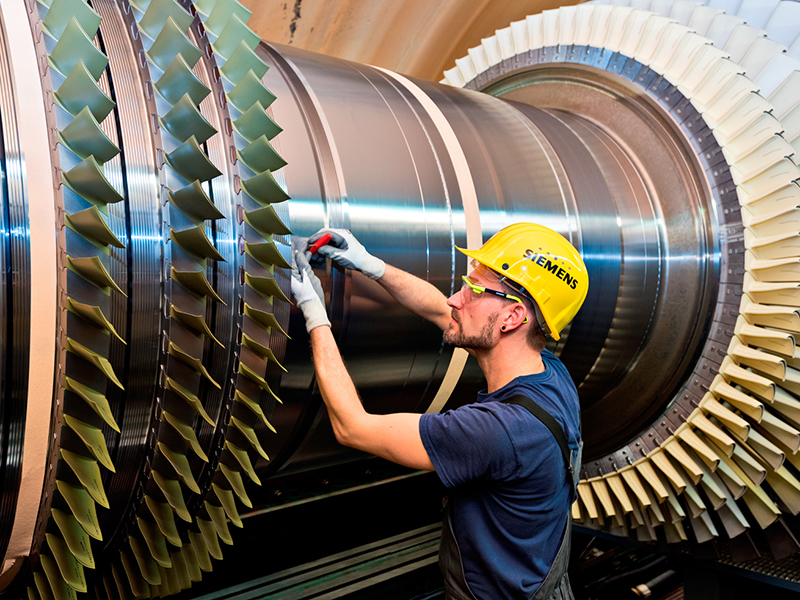
Product name: | High-Temperature Alloy Forging for Engine Turbine Blades |
Keywords: | High-Temperature Alloy Forging, Precision Forging Process, Forged Turbine Blades |
Industry: | Transportation - Aerospace industry |
Process: | Forging - Others |
Material: | Alloy steel |
Processing manufacturer
- There are 39 manufacturers that provide similar products
- There are 194 manufacturers that provide this processing technology
- There are 104 manufacturers that provide this material processing service
- There are 174 manufacturers that provide this industry processing service
Product details
Turbine blades are core components of aero-engines and gas turbines, enduring extreme conditions of high temperature, high pressure, and high-speed rotation for extended periods. To ensure their performance and reliability, high-temperature alloy forging technology has become a crucial process in manufacturing turbine blades.
High-temperature alloys (such as nickel-based and cobalt-based alloys) possess excellent high-temperature strength, oxidation resistance, and creep resistance. Through precision forging processes, alloy grain refinement can be achieved, enhancing mechanical properties while reducing internal defects. During the forging process, precise control of temperature, deformation rate, and cooling rate is necessary to ensure structural homogeneity and dimensional accuracy. Furthermore, advanced techniques such as isothermal forging and hot die forging further improve the fatigue life and high-temperature resistance of the blades.
Forged turbine blades not only outperform cast blades but also reduce material waste and lower costs. As aero-engines evolve towards higher thrust-to-weight ratios, high-temperature alloy forging technology will continue to be optimized, providing critical support for the manufacturing of next-generation turbine blades.
High-temperature alloys (such as nickel-based and cobalt-based alloys) possess excellent high-temperature strength, oxidation resistance, and creep resistance. Through precision forging processes, alloy grain refinement can be achieved, enhancing mechanical properties while reducing internal defects. During the forging process, precise control of temperature, deformation rate, and cooling rate is necessary to ensure structural homogeneity and dimensional accuracy. Furthermore, advanced techniques such as isothermal forging and hot die forging further improve the fatigue life and high-temperature resistance of the blades.
Forged turbine blades not only outperform cast blades but also reduce material waste and lower costs. As aero-engines evolve towards higher thrust-to-weight ratios, high-temperature alloy forging technology will continue to be optimized, providing critical support for the manufacturing of next-generation turbine blades.
Previous article : High-Precision Stamping Die Plate
Next article : Steel Structures in Office Building Construction
Similar products
MoreMachining Process Analysis of Carbon Steel Fixed Anchor Plates
- Process : Machining - CNC milling or milling machining
- Material : Carbon steel
What are the machining processes used for processing axial fan housings
- Process : Sheet metal - Welding
- Material : Carbon steel
Custom Fabrication of S355JR Welded H-Beams for Construction Projects
- Process : Sheet metal - Welding
- Material : Carbon steel
Cone Crusher Mantle
- Process : -
- Material :
Heavy-Walled Flange Milling-Turning Machining and Flaw Detection
- Process : Machining - Turning Milling compound
- Material : Alloy steel
Drill Stabilizers Applied in Oil Drilling Platforms
- Process : Machining - Five-axis machining
- Material : Alloy steel
Precision Machining of U-Steel Profiles for Building Applications
- Process : Stamping - General stamping
- Material : Aluminum
Innovative skiving technology: Breaking through the bottleneck of high-density heat dissipation technology
- Process : Surface treatment - Others
- Material : Alloy steel
More products
MoreMachining Process Analysis of Carbon Steel Fixed Anchor Plates
- Process : Machining - CNC milling or milling machining
- Material : Carbon steel
What are the machining processes used for processing axial fan housings
- Process : Sheet metal - Welding
- Material : Carbon steel
Custom Fabrication of S355JR Welded H-Beams for Construction Projects
- Process : Sheet metal - Welding
- Material : Carbon steel
Cone Crusher Mantle
- Process : -
- Material :
Heavy-Walled Flange Milling-Turning Machining and Flaw Detection
- Process : Machining - Turning Milling compound
- Material : Alloy steel
Drill Stabilizers Applied in Oil Drilling Platforms
- Process : Machining - Five-axis machining
- Material : Alloy steel
Precision Machining of U-Steel Profiles for Building Applications
- Process : Stamping - General stamping
- Material : Aluminum
Innovative skiving technology: Breaking through the bottleneck of high-density heat dissipation technology
- Process : Surface treatment - Others
- Material : Alloy steel