Finned Tubes, SA210-C Finned Tubes for Heat Exchangers
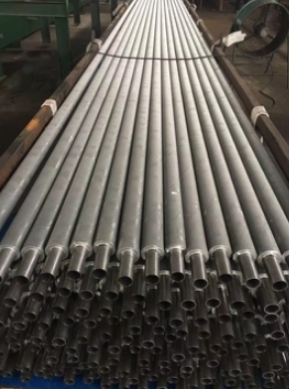
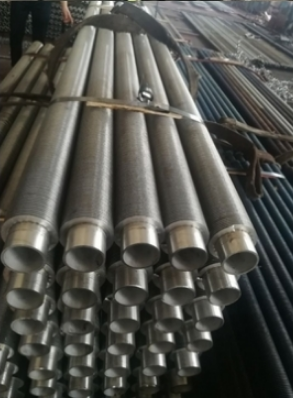
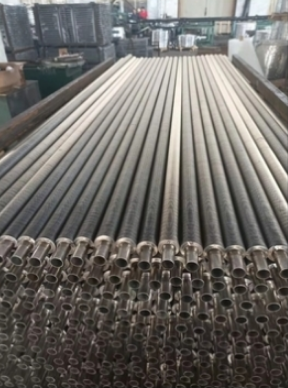
Product name: | Finned Tubes, SA210-C Finned Tubes for Heat Exchangers |
Keywords: | Finned Tubes |
Industry: | Industrial design and manufacturing services - Industry and Engineering design services |
Process: | Stamping - Precision stamping |
Material: | Alloy steel |
Processing manufacturer
- There are 33 manufacturers that provide similar products
- There are 160 manufacturers that provide this processing technology
- There are 88 manufacturers that provide this material processing service
- There are 149 manufacturers that provide this industry processing service
Product details
A finned tube is a heat exchange element. To improve heat exchange efficiency, fins are usually added to the surface of the heat exchange tube to increase the outer surface area (or inner surface area) of the heat exchange tube, thereby achieving the purpose of improving heat exchange efficiency. This is a finned tube.
Henan Bhibo specializes in the production and customization of various finned tubes.
1. Material Selection
Base Tube Material:
Carbon Steel (low cost, suitable for general industrial heat exchange);
Stainless Steel (corrosion resistant, food/pharmaceutical industry);
Copper/Aluminum Alloy (high thermal conductivity, low temperature heat exchange).
Fin Material:
Aluminum Fins (lightweight, high thermal conductivity);
Copper Fins (corrosion resistant, good electrical conductivity);
Stainless Steel Fins (high temperature/corrosive environments).
2. Fin Type and Process
High-Frequency Welded Finned Tubes: High strength, suitable for high-pressure scenarios (such as boilers, petrochemicals).
L-type/LL-type Wound Fins: Low cost, suitable for medium and low temperature heat exchange (air conditioning, waste heat recovery).
Integral Rolled Fins: No contact thermal resistance, long life (high temperature exhaust gas treatment).
Internal Finned Tubes: Enhance heat exchange inside the tube (liquid heating in chemical processes).
3. Customization Capabilities
Customizable fin height (5-20mm), spacing (2-10mm), tube diameter (10-100mm), and length.
Provides special coatings (galvanized, aluminized) to enhance corrosion resistance.
Henan Bhibo specializes in the production and customization of various finned tubes.
1. Material Selection
Base Tube Material:
Carbon Steel (low cost, suitable for general industrial heat exchange);
Stainless Steel (corrosion resistant, food/pharmaceutical industry);
Copper/Aluminum Alloy (high thermal conductivity, low temperature heat exchange).
Fin Material:
Aluminum Fins (lightweight, high thermal conductivity);
Copper Fins (corrosion resistant, good electrical conductivity);
Stainless Steel Fins (high temperature/corrosive environments).
2. Fin Type and Process
High-Frequency Welded Finned Tubes: High strength, suitable for high-pressure scenarios (such as boilers, petrochemicals).
L-type/LL-type Wound Fins: Low cost, suitable for medium and low temperature heat exchange (air conditioning, waste heat recovery).
Integral Rolled Fins: No contact thermal resistance, long life (high temperature exhaust gas treatment).
Internal Finned Tubes: Enhance heat exchange inside the tube (liquid heating in chemical processes).
3. Customization Capabilities
Customizable fin height (5-20mm), spacing (2-10mm), tube diameter (10-100mm), and length.
Provides special coatings (galvanized, aluminized) to enhance corrosion resistance.
Previous article : U-Tubes, 316L & 304 & T5 & SA179 & T11 U-Tubes for Heat Exchangers
Next article : Hot Work Die Steel for Production of Pipes, Profiles, etc.
Similar products
MoreWhat are the machining processes used for processing axial fan housings
- Process : Sheet metal - Welding
- Material : Carbon steel
Machining Process Analysis of Carbon Steel Fixed Anchor Plates
- Process : Machining - CNC milling or milling machining
- Material : Carbon steel
Cone Crusher Mantle
- Process : -
- Material :
Precision Machining of U-Steel Profiles for Building Applications
- Process : Stamping - General stamping
- Material : Aluminum
Custom Fabrication of S355JR Welded H-Beams for Construction Projects
- Process : Sheet metal - Welding
- Material : Carbon steel
Heavy-Walled Flange Milling-Turning Machining and Flaw Detection
- Process : Machining - Turning Milling compound
- Material : Alloy steel
Drill Stabilizers Applied in Oil Drilling Platforms
- Process : Machining - Five-axis machining
- Material : Alloy steel
Innovative skiving technology: Breaking through the bottleneck of high-density heat dissipation technology
- Process : Surface treatment - Others
- Material : Alloy steel
More products
MoreWhat are the machining processes used for processing axial fan housings
- Process : Sheet metal - Welding
- Material : Carbon steel
Machining Process Analysis of Carbon Steel Fixed Anchor Plates
- Process : Machining - CNC milling or milling machining
- Material : Carbon steel
Cone Crusher Mantle
- Process : -
- Material :
Precision Machining of U-Steel Profiles for Building Applications
- Process : Stamping - General stamping
- Material : Aluminum
Custom Fabrication of S355JR Welded H-Beams for Construction Projects
- Process : Sheet metal - Welding
- Material : Carbon steel
Heavy-Walled Flange Milling-Turning Machining and Flaw Detection
- Process : Machining - Turning Milling compound
- Material : Alloy steel
Drill Stabilizers Applied in Oil Drilling Platforms
- Process : Machining - Five-axis machining
- Material : Alloy steel
Innovative skiving technology: Breaking through the bottleneck of high-density heat dissipation technology
- Process : Surface treatment - Others
- Material : Alloy steel