Analysis of the Advantages and Disadvantages of Wear-Resistant Spiral Blades
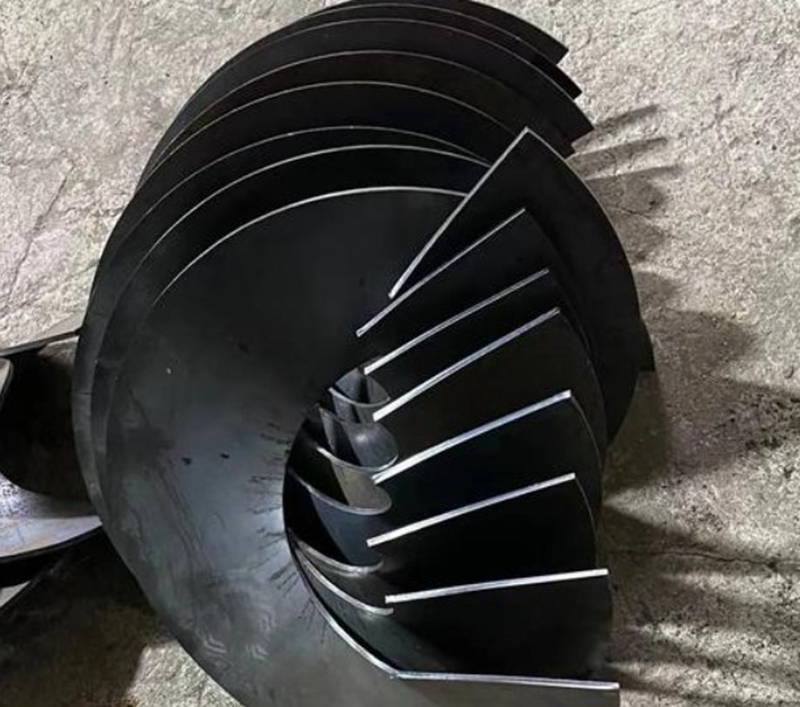
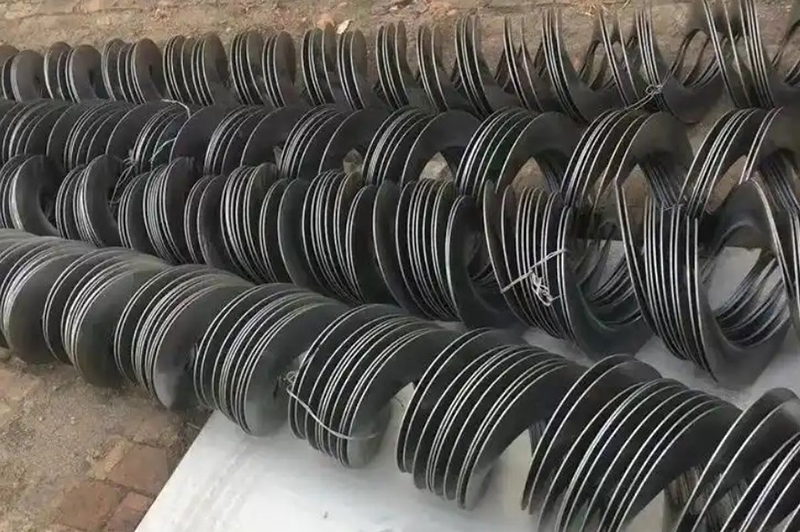
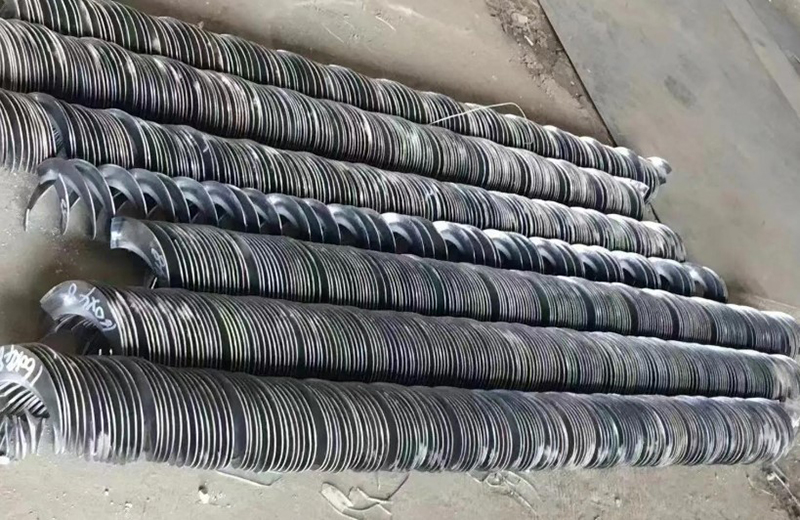
Product name: | Analysis of the Advantages and Disadvantages of Wear-Resistant Spiral Blades |
Keywords: | |
Industry: | Metallurgy and minerals - Mining industry |
Process: | - |
Material: |
Processing manufacturer
- There are 37 manufacturers that provide similar products
- There are 121 manufacturers that provide this processing technology
- There are 107 manufacturers that provide this material processing service
- There are 113 manufacturers that provide this industry processing service
Product details
Wear-resistant spiral blades are a key design for improving equipment life and operating efficiency in many high-wear applications (such as crushers, screw conveyors for abrasive materials, etc.). However, like all engineering choices, it comes at a cost. The following is a detailed analysis of the advantages and disadvantages of wear-resistant spiral blades:
Core Objective: To significantly slow down the wear rate of blades in harsh wear environments by increasing the hardness, wear resistance of the blade material, or by applying special surface treatments.
Advantages:
Significantly Extends Service Life:
Greatest Advantage: This is the fundamental purpose of choosing wear-resistant blades. Compared to ordinary carbon steel or low-alloy steel blades, wear-resistant blades can last several times longer (e.g., 2-5 times or even more) when conveying or processing abrasive materials (such as mineral sand, slag, gravel, domestic waste containing sand, and industrial waste containing metal fragments). This significantly reduces the risk of equipment downtime, reduced efficiency, or even failure due to excessive blade wear.
Value Realization: Reduces spare parts inventory, reduces replacement frequency and labor costs, which is of great significance for continuous production.
Maintains Equipment Performance and Efficiency:
New spiral blades typically have precise pitch and outer diameter dimensions to ensure optimal conveying efficiency and forced feeding. Wear-resistant blades can maintain the designed geometric dimensions for a longer period of time, avoiding problems such as reduced feed rate, decreased conveying efficiency, material backflow, and energy waste caused by blade wear and thinning, rounded blade edges, or changes in pitch. The equipment can maintain its designed processing capacity and efficiency for a long time.
Reduces Maintenance Frequency and Downtime:
Wear is the most common failure mode of spiral blades. Wear-resistant blades greatly extend the interval between replacements or repairs, significantly reducing unplanned downtime and maintenance frequency, and improving the overall operating rate and production reliability of the equipment.
Reduces Long-Term Operating Costs (in some cases):
Although the initial purchase cost of wear-resistant blades is usually higher, their ultra-long service life means that the cost allocated to unit operating time or unit processed material may be lower over the life cycle of the equipment. Especially for critical links that handle extremely abrasive materials and operate continuously, their life cycle cost (LCC) is often better than the total cost of frequently replacing ordinary blades (including blade costs, replacement labor hours, downtime losses, etc.).
Improves Adaptability to Harsh Materials:
Enables equipment to handle more reliably and economically extremely abrasive materials that traditional blades cannot withstand, expanding the application range of the equipment.
Disadvantages:
Higher Initial Cost:
Most Significant Disadvantage: Whether using high-grade wear-resistant steel plates (such as Hardox 450, NM450), casting high-chromium cast iron blades, or using hardfacing wear-resistant layers, the raw material costs and manufacturing costs are significantly higher than ordinary steel (such as Q235, Q345). For purchasers with limited budgets, the initial investment pressure is greater.
Increased Manufacturing Difficulty:
High Material Hardness: Wear-resistant materials (especially high-chromium cast iron, hardened steel plates) have high hardness and strength, which places higher demands on cutting, forming (plate rolling), drilling, and welding processes, requiring more specialized equipment (such as plasma/laser cutting) and skilled workers. Processing efficiency is usually lower.
Welding Challenges: Welding of high-hardness materials is prone to cracking, often requiring preheating, strict control of line energy, the use of special welding materials, and post-weld insulation/slow cooling measures, which increases welding complexity and cost. For hardfaced blades, the hardfacing process itself has high technical requirements and quality control requirements.
Machinability: Some wear-resistant materials (such as high-chromium cast iron) are almost impossible to machine using conventional methods, requiring higher manufacturing precision, and rework is difficult once errors occur.
Toughness and Impact Resistance May Be Limited (especially for some materials):
High-Chromium Cast Iron: Although its wear resistance is top-notch, it is very brittle and has very low toughness. When subjected to violent impacts from large heavy objects or metal impurities, or huge torque caused by accidental jamming, it is more prone to brittle fracture, rather than plastic deformation like ordinary steel. This is a serious disadvantage for working conditions with impact risks.
Hardened Steel Plates: Compared to ordinary steel, their toughness is usually also reduced (especially high grades such as Hardox 500/600), and their resistance to extreme impacts is not as good as tough materials (such as high-manganese steel).
Hardfacing Layer: The hard alloy hardfacing layer itself is also brittle and may chip or peel off under strong impact.
Note: Reasonable material selection and design can minimize this problem (for example, choosing high-manganese steel or high-toughness wear-resistant steel plates in areas with high impact risk).
Greater Difficulty in Repair and Restoration:
Overall Blade Damage: If a wear-resistant blade (especially an integrally cast high-chromium cast iron blade) is severely damaged (such as fractured), repair is extremely difficult and usually requires complete replacement.
Localized Hardfacing Layer Wear/Damage: Although hardfaced blades can theoretically be repaired, the hardfacing repair process is complex (requiring removal of the old weld layer, preheating, special welding materials, and post-weld treatment), and requires professional welders and equipment. On-site repair is difficult, and the wear resistance and reliability after repair may not be as good as the original state.
Cutting/Welding Restrictions: Cutting holes or welding attachments directly on installed wear-resistant blades is very difficult and can easily damage the blade itself, resulting in poor flexibility.
Increased Weight (some types):
Using thick-gauge wear-resistant steel plates or integrally cast high-chromium cast iron blades can significantly increase the weight of the blade, which places higher demands on spindle strength, bearing selection, and drive power, and may increase power consumption.
Summary and Selection Recommendations:
The core advantages of wear-resistant spiral blades are: ultra-long service life, stable and lasting equipment performance, reduced maintenance downtime, and potential optimized life cycle costs.
Their main costs are: high initial investment, increased manufacturing difficulty, potential reduction in toughness (risk of improper material selection), and greater repair difficulty.
Similar products
MoreMachining Process Analysis of Carbon Steel Fixed Anchor Plates
- Process : Machining - CNC milling or milling machining
- Material : Carbon steel
Cone Crusher Mantle
- Process : -
- Material :
What are the machining processes used for processing axial fan housings
- Process : Sheet metal - Welding
- Material : Carbon steel
Custom Fabrication of S355JR Welded H-Beams for Construction Projects
- Process : Sheet metal - Welding
- Material : Carbon steel
Drill Stabilizers Applied in Oil Drilling Platforms
- Process : Machining - Five-axis machining
- Material : Alloy steel
Precision Machining of U-Steel Profiles for Building Applications
- Process : Stamping - General stamping
- Material : Aluminum
Heavy-Walled Flange Milling-Turning Machining and Flaw Detection
- Process : Machining - Turning Milling compound
- Material : Alloy steel
Innovative skiving technology: Breaking through the bottleneck of high-density heat dissipation technology
- Process : Surface treatment - Others
- Material : Alloy steel
More products
MoreMachining Process Analysis of Carbon Steel Fixed Anchor Plates
- Process : Machining - CNC milling or milling machining
- Material : Carbon steel
Cone Crusher Mantle
- Process : -
- Material :
What are the machining processes used for processing axial fan housings
- Process : Sheet metal - Welding
- Material : Carbon steel
Custom Fabrication of S355JR Welded H-Beams for Construction Projects
- Process : Sheet metal - Welding
- Material : Carbon steel
Drill Stabilizers Applied in Oil Drilling Platforms
- Process : Machining - Five-axis machining
- Material : Alloy steel
Precision Machining of U-Steel Profiles for Building Applications
- Process : Stamping - General stamping
- Material : Aluminum
Heavy-Walled Flange Milling-Turning Machining and Flaw Detection
- Process : Machining - Turning Milling compound
- Material : Alloy steel
Innovative skiving technology: Breaking through the bottleneck of high-density heat dissipation technology
- Process : Surface treatment - Others
- Material : Alloy steel