Analysis of Machining Processes for Biomass Boiler Shell Manufacturing
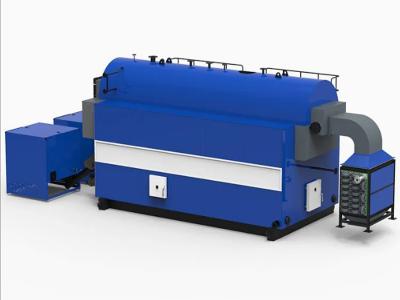
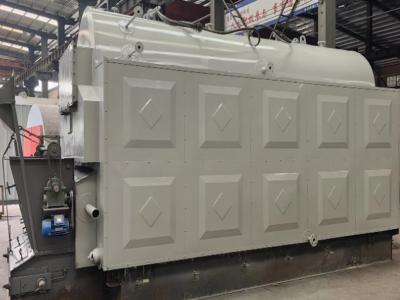
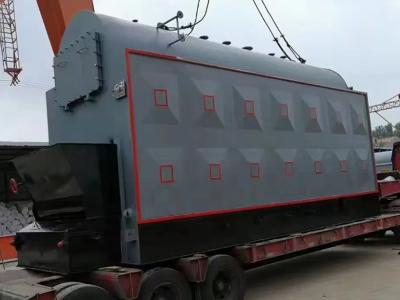
Product name: | Analysis of Machining Processes for Biomass Boiler Shell Manufacturing |
Keywords: | Biomass Boiler, Shell Manufacturing Technology, Machining Process, Precision Blanking, Forming Process |
Industry: | Mechanical and electrical - Boiler industry |
Process: | Machining - CNC milling or milling machining |
Material: | Carbon steel |
Processing manufacturer
- There are 57 manufacturers that provide similar products
- There are 190 manufacturers that provide this processing technology
- There are 95 manufacturers that provide this material processing service
- There are 133 manufacturers that provide this industry processing service
Product details
The biomass boiler shell, as a core component bearing high-temperature and high-pressure conditions, directly affects the boilers energy efficiency and safety. The following analyzes key technical points from the perspective of machining processes to help the industry optimize production processes.
I. Precision Blanking and Forming Process
High-precision cutting of Q245R boiler steel, 316L stainless steel, and other plates is performed using laser cutting or CNC plasma cutting, controlling dimensional deviations ≤±0.5mm to ensure subsequent splicing accuracy. Circular arc / right-angle bending is completed by CNC bending machines, and stiffeners, observation holes, and other structures are processed with mold stamping to improve shell rigidity and functionality.
II. Welding Process and Sealing Guarantee
The shell is spliced using fully automatic argon arc welding or submerged arc welding. For thick plates (≥10mm), multi-layer and multi-pass welding is implemented, preheating to 150-200℃ before welding, and RT X-ray inspection is performed after welding to ensure that the weld has no pores or cracks. The airtightness test pressure is 1.5 times the working pressure to eliminate the risk of flue gas leakage.
III. Precision Machining and Surface Treatment
Key parts such as flange sealing surfaces and nozzle bevels are precision machined by CNC lathes / milling machines, with surface roughness controlled below Ra1.6μm to ensure component assembly accuracy. Finally, sandblasting and rust removal + high-temperature resistant coating (such as aluminum-silicon coating) are performed, with temperature resistance up to 600℃ or more, significantly improving the shells corrosion resistance and oxidation resistance.
IV. Core Points of Quality Control
- Dimensional Accuracy: Key hole spacing (deviation ≤±0.3mm) and roundness error (≤0.1% D) are detected using a coordinate measuring machine;
- Mechanical Properties: Tensile / bending tests are performed on samples, and the weld strength must be ≥85% of the base material;
- Reliability Testing: High-temperature pressure-bearing tests are performed simulating biomass combustion conditions to verify the long-term operational stability of the shell.
Biomass boiler shell manufacturing needs to take into account high-temperature resistance, corrosion resistance, and structural strength. Through CNC and automated machining processes, production efficiency and product quality can be effectively improved, providing a solid guarantee for the efficient operation of clean energy equipment.
Similar products
MoreMachining Process Analysis of Carbon Steel Fixed Anchor Plates
- Process : Machining - CNC milling or milling machining
- Material : Carbon steel
Custom Fabrication of S355JR Welded H-Beams for Construction Projects
- Process : Sheet metal - Welding
- Material : Carbon steel
Cone Crusher Mantle
- Process : -
- Material :
What are the machining processes used for processing axial fan housings
- Process : Sheet metal - Welding
- Material : Carbon steel
Precision Machining of U-Steel Profiles for Building Applications
- Process : Stamping - General stamping
- Material : Aluminum
Heavy-Walled Flange Milling-Turning Machining and Flaw Detection
- Process : Machining - Turning Milling compound
- Material : Alloy steel
Drill Stabilizers Applied in Oil Drilling Platforms
- Process : Machining - Five-axis machining
- Material : Alloy steel
Innovative skiving technology: Breaking through the bottleneck of high-density heat dissipation technology
- Process : Surface treatment - Others
- Material : Alloy steel
More products
MoreMachining Process Analysis of Carbon Steel Fixed Anchor Plates
- Process : Machining - CNC milling or milling machining
- Material : Carbon steel
Custom Fabrication of S355JR Welded H-Beams for Construction Projects
- Process : Sheet metal - Welding
- Material : Carbon steel
Cone Crusher Mantle
- Process : -
- Material :
What are the machining processes used for processing axial fan housings
- Process : Sheet metal - Welding
- Material : Carbon steel
Precision Machining of U-Steel Profiles for Building Applications
- Process : Stamping - General stamping
- Material : Aluminum
Heavy-Walled Flange Milling-Turning Machining and Flaw Detection
- Process : Machining - Turning Milling compound
- Material : Alloy steel
Drill Stabilizers Applied in Oil Drilling Platforms
- Process : Machining - Five-axis machining
- Material : Alloy steel
Innovative skiving technology: Breaking through the bottleneck of high-density heat dissipation technology
- Process : Surface treatment - Others
- Material : Alloy steel